目次
工場の受付と入退館管理の効率化は自動化だけでは解決できない?
工場の入退館管理は、多くの取引先や来訪者が頻繁に訪れるため、受付業務が非常に混雑しがちです。特に、大人数での来訪や、期間指定の入館証の発行が必要となる搬入や工事関連の受付業務では、一般的な自動受付システムでは対応が難しいケースが多く見られます。こうした業務の効率化には、より高度な自動化ソリューションが求められています。
工場におけるセキュリティと安否確認の重要性
工場の入退館管理においては、来訪者のセキュリティ管理が最重要課題です。加えて、災害や事故が発生した際には、来訪者や従業員の安否確認を迅速に行うための記録保持が不可欠です。しかし、現状では、受付業務を警備担当者が兼任したり、記録保持を複数の社員が分担するなど、非効率な運用が続いており、工数の負担が大きくなっています。こうした状況を改善するためには、デジタル化による記録保持と管理の一元化が求められています。
現場からでも効率的な連携を可能にするコミュニケーションツールの活用
工場の受付業務では、窓口担当者が現場に出ていることも多く、迅速に連絡が取れる仕組みが求められます。これに対応するため、TeamsやSlackなどのコミュニケーションツールと連携し、来訪者の対応や受付業務の効率化を図るソリューションが導入されています。これにより、受付担当者は現場にいながらでも、スマホやPCを通じて時間や場所を問わずスムーズに受付対応が可能になります。
受付業務のデジタル化と自動化がもたらす業務効率化
工場の受付業務の効率化には、複数の業務を統合的に自動化できるソリューションが必要です。例えば、入館証の自動発行や入退館履歴の記録、定期的な出入り業者の管理などをデジタル化することで、これまで手動で行っていた業務を大幅に効率化することができます。こうしたソリューションにより、ペーパーレスでの運用や、業務プロセスの最適化が実現し、セキュリティと業務効率の向上が期待できます。
工場特有の課題に対応した受付自動化ソリューションの解説
今回のセミナーでは、工場の特有の課題に対応した受付自動化ソリューション「Smart at Reception for FACTORY」を紹介し、入退館管理の課題解決方法を詳しく解説します。このソリューションは、工場の受付ニーズに応えるため、来訪者全員の入退館履歴の記録機能や入館証の発行機能を備え、さらに特定の項目をカスタマイズすることが可能です。また、定期的に出入りする業者向けの管理機能も充実しており、工場に特化した効率化を支援します。
工場の受付業務の効率化を検討中の方へ
工場の受付業務の効率化に課題を感じている方や、特定の業務改善ニーズをお持ちの方に向けて、実際の事例を交えながら具体的な解決策を提案します。貴社の工場特有の課題をデジタル技術と自動化ソリューションでどう解決できるか、ぜひこの機会にご参加ください。
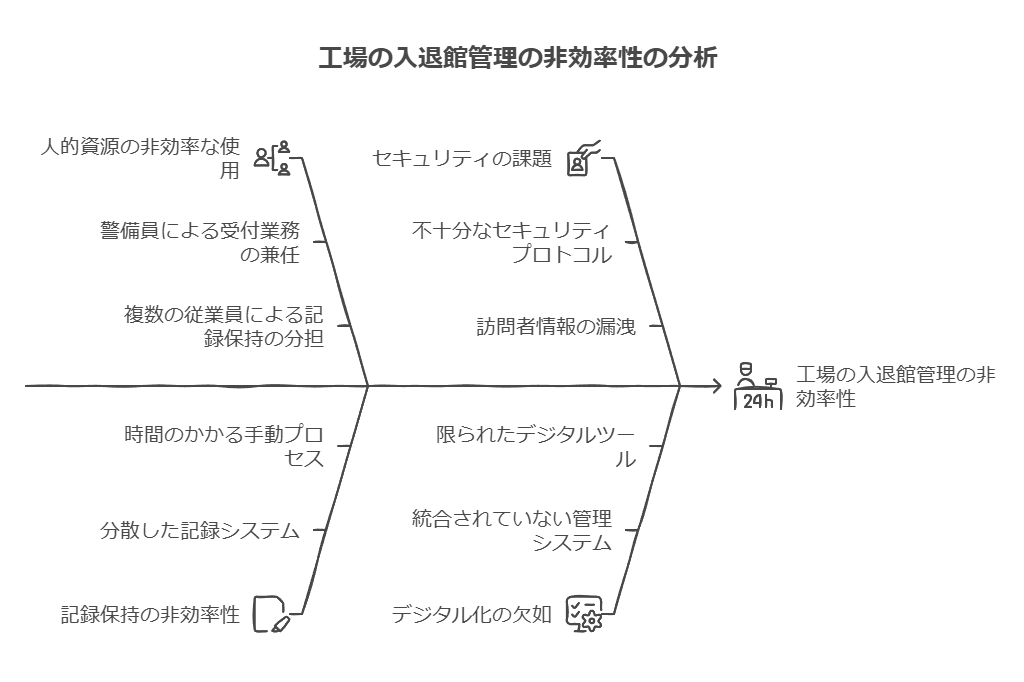
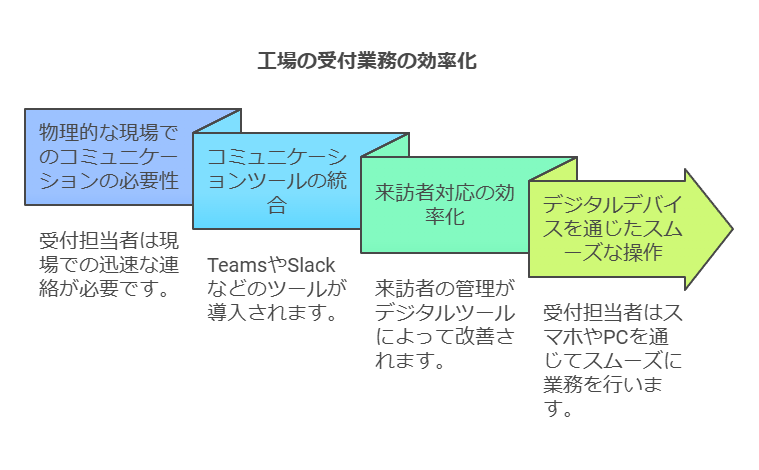
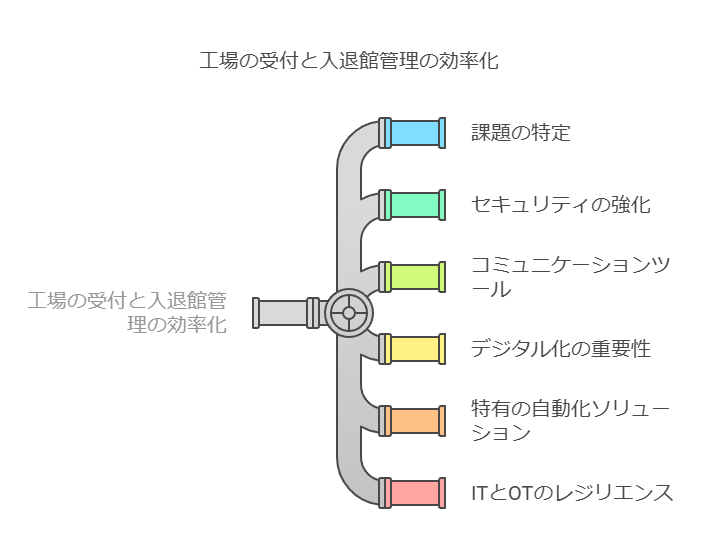
製造業におけるITとOTのレジリエンスを強化するサイバープロテクション
製造業のIT(情報技術)とOT(運用技術)におけるリスク軽減のためには、データ保護の強化が不可欠です。具体的には、定期的なデータバックアップ、安全なストレージの確保、アクセス制御の強化、データ暗号化、従業員トレーニングの実施、サイバーセキュリティ対策の導入、そして災害復旧計画の策定が求められます。これらの対策を実施することで、製造現場のレジリエンスが向上し、サイバー攻撃やその他のリスクから組織を守ることが可能となります。
私たちは、最新のサイバー脅威の状況に対応し、OTや産業制御システム(ICS)に求められるセキュリティ要件を満たすために、製造業におけるデータ保護の方法を詳しく解説しています。また、これらのリスクに対抗するための包括的なサイバープロテクションサービスも提供しており、製造業のITおよびOT環境のセキュリティを包括的にサポートします。
セキュリティ課題を抱える製造業のためのソリューション
IoTの普及により、製造現場の環境はますますオープン化し、制御システムのセキュリティ対策が以前にも増して重要となっています。従来の工場では、制御システムはクローズドな環境で運用されていましたが、IoTの導入により、これらのシステムが外部との接続を持つようになり、ウィルス感染や不正アクセスなどのサイバー攻撃のリスクが飛躍的に高まっています。このような攻撃が成功すると、工場の稼働停止による大規模な経済的損害や、社会的信用の失墜といった深刻な影響をもたらす可能性があります。
制御システムのセキュリティ対策の難しさと重要性
制御システムのセキュリティ対策は、通常の情報システムとは異なるアプローチが必要です。情報システムでは主に「情報」を保護の対象としていますが、制御システムでは「モノ」(設備や製品)を対象とするため、セキュリティの思想や対策方法も異なります。製造業の制御システムには、リアルタイムでの運用が求められるため、停止させることなくセキュリティを確保することが重要です。また、制御システムにおけるセキュリティの脆弱性は、企業全体の運用に大きな影響を与えるため、ITとOTの統合的なセキュリティ対策が求められます。
これにより、製造業のITとOTに対するセキュリティ対策の重要性が強調され、具体的な解決策とその実行の必要性が明確に示されています。また、データコンサルタントとして、製造業のニーズに合わせた包括的なサイバーセキュリティのアプローチが提案されています。
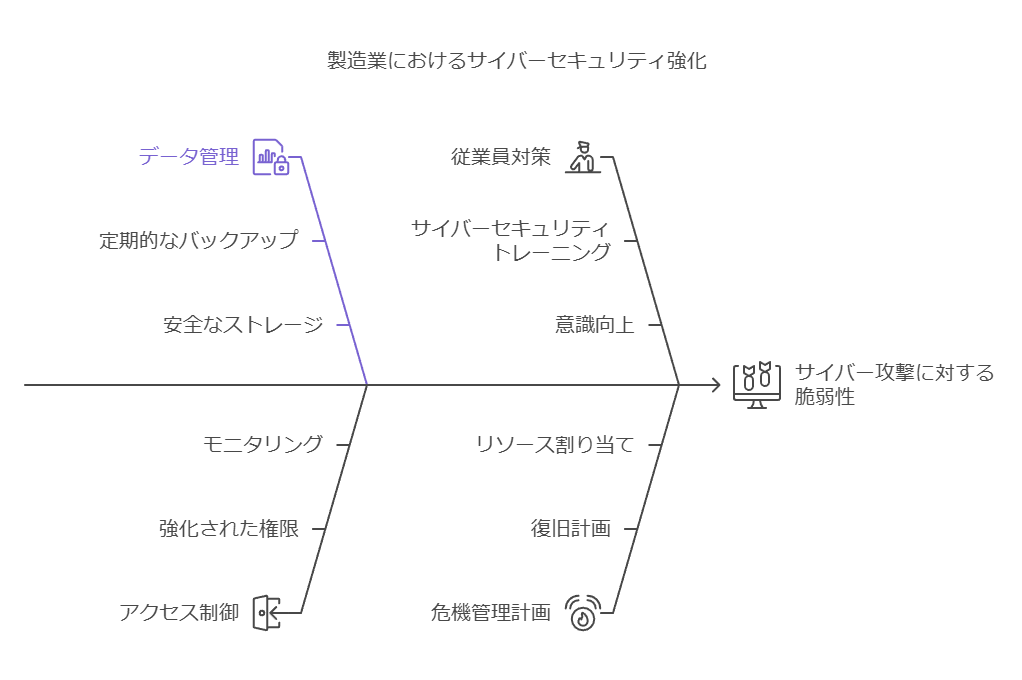
ネットワーク化の推進により、製造業界において様々なメリットが得られています。これらのメリットは、データの収集から生産プロセスの最適化、さらには新たなビジネスモデルの創出に至るまで、多岐にわたります。
1. モニタリング用データの収集効率向上とコスト削減
ネットワーク化によって、工場内の機器やセンサーからリアルタイムでデータを収集できるようになり、モニタリングの精度が向上します。また、手作業によるデータ収集の必要性が減り、コストの削減が実現されました。
2. 生産自動化領域の拡大
ネットワーク化により、製造プロセスのさらなる自動化が進みました。これにより、手作業に依存する工程が削減され、生産効率が向上しました。
3. 生産リードタイムの短縮
リアルタイムデータの活用によって、製造工程の迅速な調整が可能となり、生産リードタイムが大幅に短縮されました。これにより、顧客への迅速な納品が可能になり、競争力が強化されます。
4. 生産ラインの作業人員の最適化
ネットワーク化された自動化システムの導入により、作業人員の最適配置が可能となり、労働力の削減と同時に効率的な運用が実現されました。
5. 製品歩留まりの向上
ネットワークによるデータ分析とモニタリングの強化により、不良品の発生を減少させ、製品歩留まりが向上しました。これにより、資源の無駄が削減され、生産効率がさらに向上します。
6. メンテナンス回数の削減
予知保全の導入により、計画的なメンテナンスが可能になり、機器のダウンタイムが減少しました。これにより、メンテナンスコストの削減が実現されました。
7. 生産ライン組み換え時間の短縮
ネットワーク化により、生産ラインの組み換えが迅速に行えるようになり、柔軟な生産対応が可能となりました。これにより、顧客の多様なニーズに迅速に応えることができるようになりました。
8. 作業員の教育コスト削減
自動化システムとネットワーク化により、作業の標準化が進み、新規作業員の教育が簡素化されました。これにより、教育コストの削減が実現されました。
9. データの見える化によるカイゼン活動の品質向上
ネットワーク化により、工場内のデータが一元化され、見える化が進みました。これにより、カイゼン活動の精度と品質が向上し、継続的な改善が可能となります。
10. 工場間の生産調整と仕向地変更の容易化
ネットワークによって、複数の工場間での生産調整がスムーズに行えるようになり、柔軟な仕向地変更が可能となりました。これにより、需給バランスの最適化が実現されます。
11. 遠隔地コミュニケーションの向上
工場-工場間や工場-本社間の遠隔地コミュニケーションがネットワーク化により大幅に向上し、効率的な意思決定が可能となりました。
12. 新たなビジネスモデルの創出
ネットワーク化されたデータを活用することで、新たなビジネスモデルの創出が可能となり、付加価値の高い製品やサービスの提供が実現されました。
「つながる工場」「工場内ネットワーク」への取り組みの背景
企業がIoTを活用した「つながる工場」や「工場内ネットワーク」に取り組むきっかけは、多岐にわたります。
経営層からの指示(トップダウン): 経営層が企業の競争力を維持・強化するために、ネットワーク化を推進する決定を下すケースが増えています。
現場からの声(ボトムアップ): 現場からの生産性向上や効率化のニーズに応えるため、ネットワーク化が進められています。
企業競争力の維持・強化のため: 競争力のある企業であり続けるためには、デジタル化やネットワーク化が必須となっています。
顧客要件としてのニーズ: 顧客からの購買条件として、工場のネットワーク化やデータ活用が求められるケースも増えています。
国際的な規制への対応: 国際的な規制や基準に準拠するために、ネットワーク化が必要となる場合があります。
この1年で進展した工場ネットワークの領域
ネットワーク化に関して、製造業界では以下の領域で進展が見られます。
自社の製造現場の機器間: 機器間のネットワーク化が進み、効率的な生産管理が実現されています。
自社の製造現場の機器と管理ツール間: 製造機器と管理ツールの連携が進み、生産プロセスの見える化が一層進展しました。
自社の管理ツールと製造システム間(MESなど): 管理ツールとMES(製造実行システム)との連携により、製造プロセスの最適化が進んでいます。
自社の製造システムと基幹システム間(オフィスシステム): 製造システムと基幹システムの連携により、生産と業務の統合が進み、企業全体の効率が向上しています。
自社の工場間での各層のシステム間(一部・全部): 工場間でのシステム連携が一部または全部で進展し、グローバルな生産体制の効率化が図られています。
他社も含めた工場間での各層のシステム間: 他社を含むサプライチェーン全体でのネットワーク連携が進み、業界全体でのデータ活用が促進されています。
これらの進展は、データコンサルタントとして製造業のネットワーク化を支援し、競争力を高めるための重要な要素として捉えることができます。
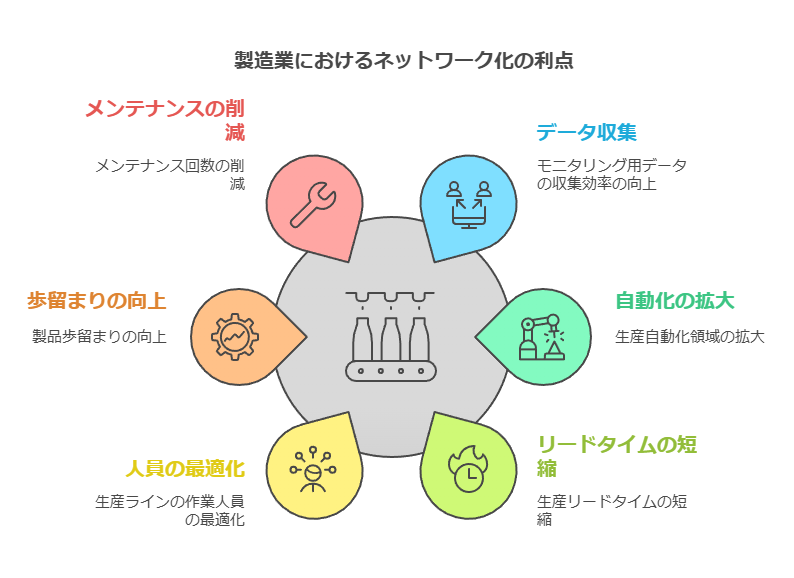
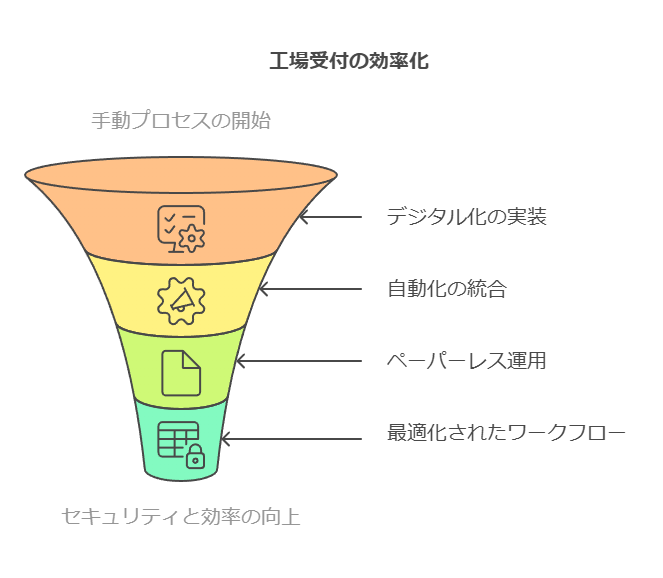
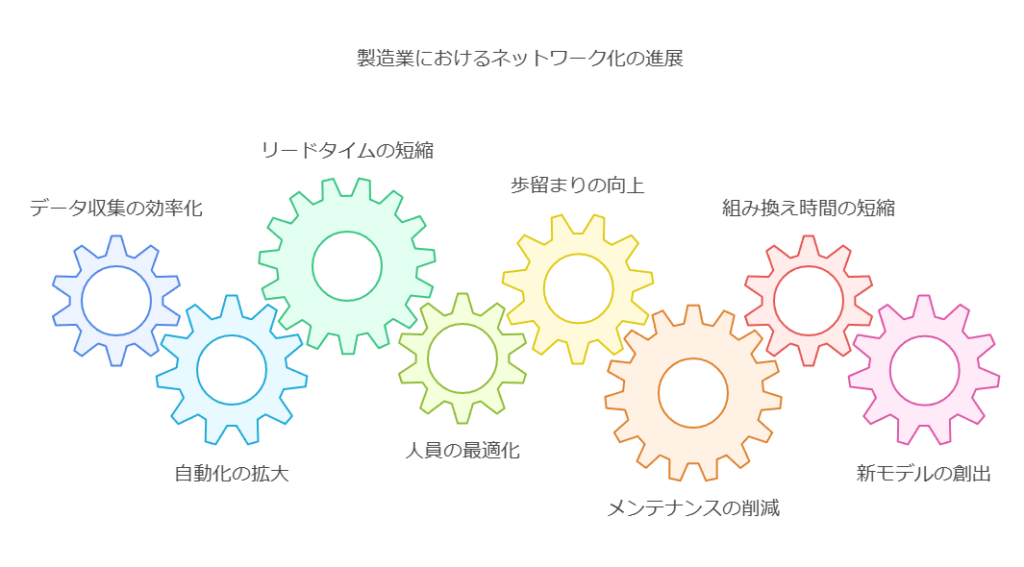
防爆エリアにおけるデジタル化の課題
防爆エリアでの特殊なデジタル化要件 可燃性ガスや危険物を取り扱う施設では、「防爆エリア」として厳格に管理されています。このエリアでのデジタル化には、多くの課題が存在します。防爆エリアでは、空気中に可燃性ガス、蒸気、または粉じんが含まれており、これらの物質は非常に高い反応性を持っています。そのため、わずかな熱や火花でも燃焼や爆発を引き起こす可能性があります。
通常の電子機器のリスク 一般的な電子機器は、通電時に発生する微細な火花や発熱、また静電気の発生などから、これらの可燃性物質の着火源となるリスクがあります。このため、防爆エリアでのデジタル化には、特別な対策が必要となります。具体的には、爆発防止のために防爆基準に準拠した特殊な機器やシステムを選定する必要があります。
防爆対応デバイスを活用したリモート保全の実現
防爆対応デバイスの導入による課題解決 防爆エリアにおけるリモート保全を実現するためには、適切な「防爆対応デバイス」の導入が不可欠です。これにより、保全作業員の安全を確保しつつ、業務効率化を図ることができます。以下に、具体的なデバイスとその活用方法をご紹介します。
振動無線センサー: 防爆基準に対応した無線センサーを使用し、設備の振動や温度を測定します。これにより、故障予知が可能となり、設備のダウンタイムを最小限に抑えることができます。
IoTカメラによるアナログ計器のデジタル化: 機械学習を活用したIoTカメラにより、アナログ計器の自動読み取りを行います。これにより、リアルタイムでのデータ収集とモニタリングが可能となります。
作業員の安全管理と位置測位: 防爆エリア内での作業員の位置を把握するための位置測位ソリューションを導入し、作業員の安全をリアルタイムで管理します。
防爆対応の無線アクセスポイント: 危険エリア内に設置可能な無線アクセスポイントを導入し、安定した通信環境を提供します。
防爆対応スマートフォンとモバイルデバイス用防爆ケース: 防爆エリア内での作業をサポートするため、防爆対応のスマートフォンやタブレットを使用し、また一般のモバイルデバイスを防爆ケースで保護することで、安全なデジタル環境を構築します。
防爆デバイスとSRMによるスマートファクトリの実現
データ集約と統合によるスマートファクトリの推進 これらの防爆対応デバイスから収集したデータは、当社が提供する「J産業IoTセキュアリモートマネジメント(SRM)」で一元管理されます。SRMを活用することで、以下のメリットを提供します:
IoTデータの可視化と分析: データをリアルタイムで可視化し、分析を行うことで、工場内の状況を正確に把握し、迅速な意思決定が可能となります。
基幹システムとの統合: 製造業の各基幹システムとデータを統合し、スマートファクトリ化をワンストップで支援します。これにより、製造プロセス全体の最適化を実現し、生産性を向上させることができます。
ここでは、防爆エリアにおけるデジタル化の課題を明確にし、具体的な防爆対応デバイスの導入と、それによるリモート保全の実現方法を段階的に説明しました。また、これらのデバイスを活用して、工場全体のデジタル化とスマートファクトリ化を推進するための包括的な提案を致します。
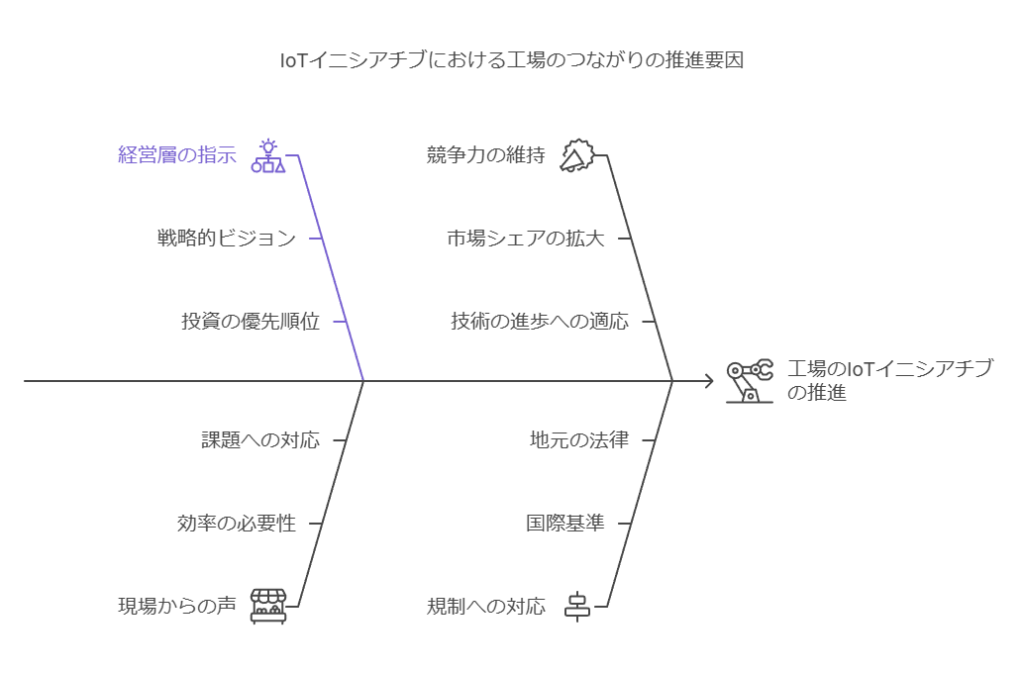
データコンサルタントの視点で、IoT技術がビジネスや社会に与える影響を強調しつつ、企業がどのようにしてこの技術を活用するか、さらに具体的に示すために、次のように文章を段階的に変更します。
IoTが求められる背景
IoT(Internet of Things)は、インターネットを介して物理的な「モノ」がデータを収集・通信し、相互に連携する技術です。これにより、従来のサーバーやパソコンなどのデジタル機器を超えて、あらゆる物理デバイスがインターネットに接続され、リアルタイムでデータをやり取りすることが可能になります。
この技術の背景には、産業構造の変化や消費者ニーズの多様化があり、企業はIoTを活用することで、新たな価値創造や業務効率化を図っています。特に、データのリアルタイムな取得と分析による迅速な意思決定は、競争優位性の確立に不可欠です。
IoT技術の主な応用例として、以下の4つの分野が挙げられますが、これに限らず、企業ごとに特有のビジネスニーズに合わせた応用が進んでいます。
モノの状態監視: IoTセンサーによるリアルタイムなモニタリングにより、製造ラインの稼働状況や設備の健康状態を継続的に監視できます。これにより、予防保全や迅速なトラブル対応が可能となり、ダウンタイムの削減やメンテナンスコストの最適化が図れます。
モノの遠隔操作: 工場やインフラの遠隔監視・制御により、場所を問わず効率的な運用が可能になります。たとえば、エネルギー管理システムの遠隔操作を通じて、エネルギー使用量の最適化やコスト削減が実現します。
モノの位置把握: ロジスティクスにおいて、IoTによるリアルタイムの位置追跡が可能となり、在庫管理や輸送の効率化が進みます。これにより、サプライチェーン全体の可視化とリードタイムの短縮が実現します。
モノ同士の連携: スマートファクトリーでは、IoTデバイス間の連携により、自動化とプロセスの最適化が進みます。たとえば、製造装置同士がデータを共有し、相互に調整することで、品質向上と生産性の向上が達成されます。
これらのIoT技術を導入することで、製造業、エネルギー、交通、農業など、多様な分野でデータ駆動型の意思決定が促進され、新たなビジネスモデルやサービスが誕生します。企業にとっては、これらの技術をいかに自社のニーズに合わせてカスタマイズし、最大限に活用するかが、競争力の鍵となります。
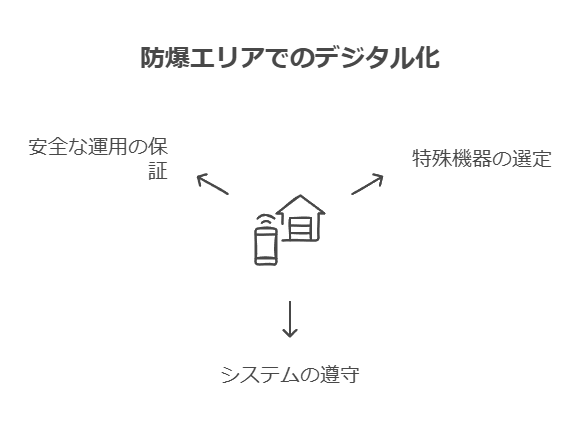
増加する無線通信機器と高まるサイバーセキュリティ対策の重要性
近年、産業機器、オフィス機器、家庭用IoT機器など無線通信機能を持つ組み込みシステムの利用が急増していることに伴い、サイバー攻撃による機能停止や情報漏えいのリスクも増大しています。特に、これらのデバイスが企業の業務や消費者の生活に深く浸透しているため、従来の機能安全対策に加え、無線通信機器に特有のサイバーセキュリティ脆弱性を低減することが不可欠です。
2025年までに求められる「RED-DA」対応と関連規格の把握
EUでは、IoT機器や産業制御システムを含む無線機器に対して、2024年8月以降に「無線機器指令委託法令(RED-DA)」の要件を満たすことが義務付けられます。この指令は、無線通信機器のセキュリティ強化を目的とし、脆弱性に対応した設計を義務化しています。企業の開発部門は、早急にこれらの規制に準拠した開発プロセスを整備する必要があります。
また、RED-DAで参照されている整合規格には「IEC 62443-4-2」や「ETSI EN 303 645」などが含まれており、これらの規格との整合性を保ちながら、機器のセキュリティ要件を満たす設計と開発が求められます。
EUサイバーレジリエンス法(CRA)の影響と対応準備の必要性
さらに、今後はネットワーク機能を持つすべての電子機器を対象とした「EUサイバーレジリエンス法(CRA)」の施行も予定されており、すべての無線通信機器に対してセキュリティ認証の取得が義務付けられる可能性があります。これにより、法案や規格に準拠した対応が求められる範囲がさらに拡大し、開発者や担当者にとってはさらなる負担増加が予想されます。
整合規格の実装アプローチと認証プロセスの効率化
これらの規制に対応するためには、無線通信機器の開発プロセスにセキュリティを組み込むアプローチが必要です。当社では、整合規格に基づいた機器の検証手法や、認証取得に必要な手続きの効率化をサポートするコンサルティングサービスを提供しています。これにより、無線通信機器の開発部門が直面する複雑な要件にも迅速に対応できるよう支援いたします。
RED-DA、IEC 62443-4-2、ETSI EN 303 645に関する疑問を解消
「RED-DAへの対応方法を知りたい」「IEC 62443-4-2/ETSI EN 303 645との関係を理解したい」「具体的な認定プロセスを把握したい」という課題を抱える開発者の方々を対象に、整合規格や具体的な認定プロセスの解説を行うセミナーを開催します。また、専門家による認証取得の支援も行っております。
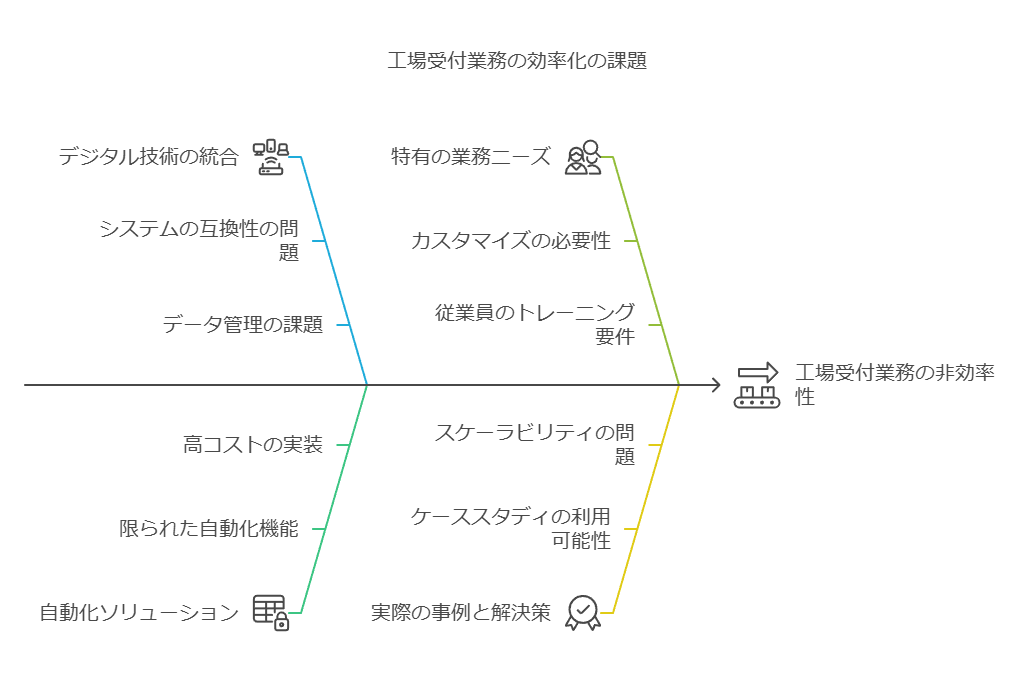
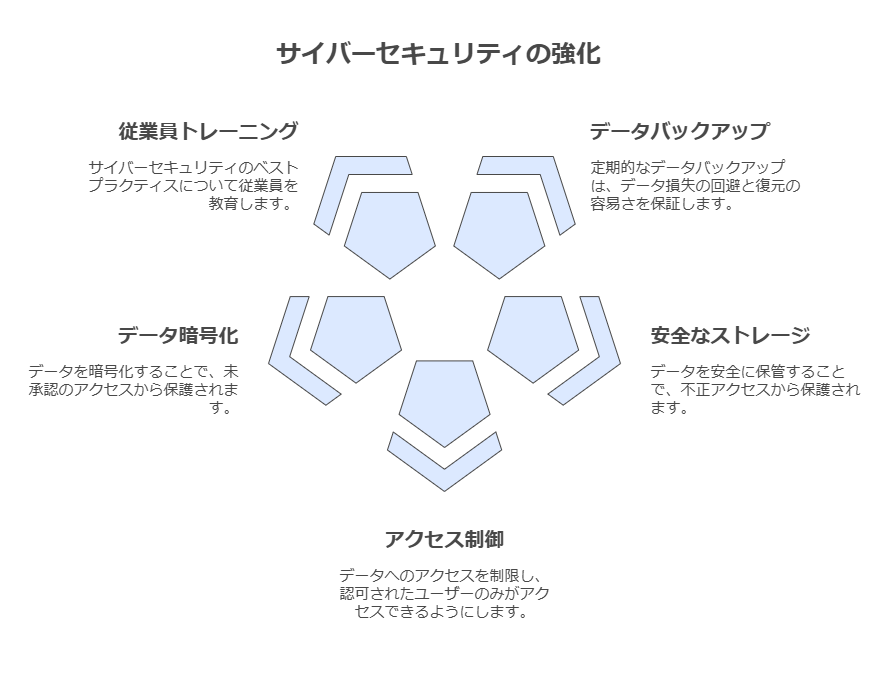
複雑なOTネットワークを効率的に管理するための実践ガイド
現代の製造業において、OT(Operational Technology)ネットワークの複雑化が進んでおり、これを効率的に管理することはセキュリティ担当者にとって大きな課題となっています。データコンサルタントの視点から、OTネットワークの資産管理や脆弱性の可視化を実現し、運用効率の向上に役立つソリューションを提案します。
具体的には、OTネットワーク内のトラフィックを解析し、デバイスや脆弱性を可視化するソフトウェアの導入が有効です。さらに、この可視化を効率化するためには、アドオンツールなどを使用し、複雑なトラフィックを効率的に集約することが重要です。
これにより、リアルタイムでのモニタリング、異常検出、脆弱性診断をワンストップで行える体制が構築されます。特に、製造業におけるOT資産管理や脆弱性の可視化に関心がある企業にとって、これらのソリューションは重要な役割を果たすでしょう。
デジタル時代におけるネットワーク安定性の重要性
デジタル化が進む現在、企業運営においてネットワークの安定性は不可欠な要素です。業務のオンライン化やデータ転送量の増加により、ネットワークの監視能力とトラブルシューティングの迅速さが、ビジネスの成功に直結しています。
しかし、従来の監視手法では、パケットキャプチャやSNMPなどを用いた監視が一般的であったものの、膨大なデータ量や詳細なトラフィック情報の即時把握が難しいという課題がありました。特に、大規模ネットワーク環境では、トラフィック分析にかかる工数が増加し、障害対応に遅れが生じやすくなっています。
効率的なネットワーク管理による迅速な障害対応
このような状況に対応するために、効率的なネットワーク管理ツールの活用が不可欠です。これにより、ネットワーク障害箇所を一目で特定し、問題を迅速に解決できるようになります。さらに、トラフィックの詳細情報、例えば「いつ・誰が・どのような通信を行ったか」などの分析が容易に行えるため、障害発生時の対応速度が劇的に向上します。
具体的な製品の活用方法やユーザーインターフェースを交えた実演により、ツール導入後の運用効率向上やトラブルシューティングの迅速化を体感していただけます。ネットワークの安定性確保やトラフィック分析の難しさにお悩みの方には、このようなソリューションの導入が最適です。
この文章では、複雑なOTネットワーク管理の課題と効率的な解決策を強調し、ネットワークの安定性向上と迅速な障害対応の重要性を明確にしました。
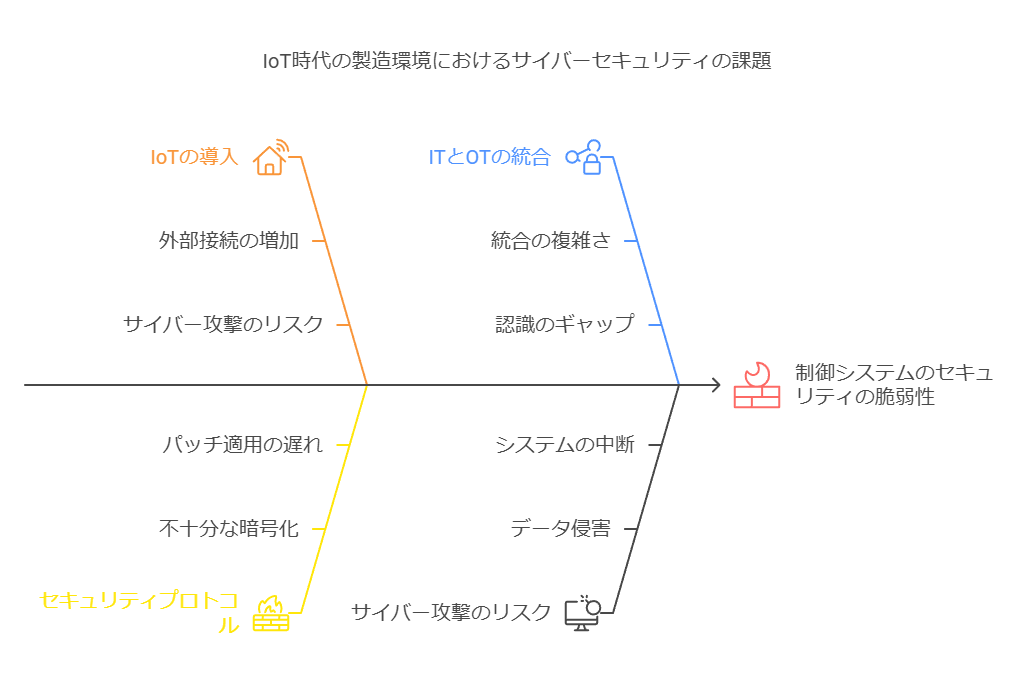
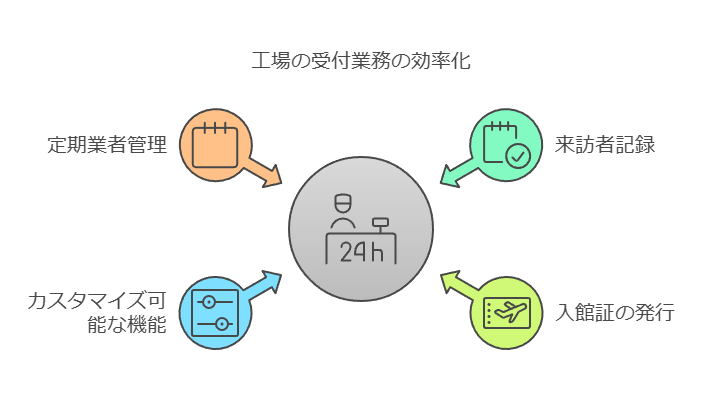
進むITとOTの融合とITネットワーク部門の役割拡大
近年、製造業界では生産性向上、品質改善、イノベーション促進を目的に、工場内の設備や装置からのリアルタイムデータを活用する取り組みが加速しています。このデジタルトランスフォーメーションの流れに伴い、従来はクローズドな環境で運用されていたOT(Operational Technology)ネットワークが外部ネットワークと接続され、ITとOTの融合が進んでいます。
しかし、この外部接続の増加により、OTネットワークがサイバー攻撃のリスクにさらされるようになっています。その結果、IT部門は従来のITシステム管理に加え、OTネットワークのセキュリティ強化という新たな役割を担うことが求められています。
IT部門がOT環境を管理するための課題
OTネットワークは、ITネットワークとは根本的に異なる特性を持っています。工場システムは、リアルタイム制御や長期間の安定運用が求められるため、頻繁なOSのパッチ適用やウイルス対策ソフトの導入が慎重に行われるケースが多いです。また、多くの設備が10年以上使用されることから、古いOSが依然として運用されており、脆弱性が蓄積されていることが少なくありません。
さらに、製造ラインのレイアウト変更や設備の入れ替えが頻繁に行われるため、現場のIT部門を介さずにシステムが構築されるケースが多く、結果としてOT管理者でさえも工場全体のシステムを把握しきれていないことがあります。
OTネットワーク管理におけるIT部門のアプローチ
IT部門がOT環境を適切に管理するためには、まず既存システムの脆弱性評価を実施し、必要に応じてセキュリティ対策やアップグレードを実施することが重要です。ただし、OTシステムへの負荷を最小限に抑えつつ、以下のような体制の強化が求められます。
リアルタイム監視と管理の強化
OTネットワーク全体のリアルタイムモニタリングを強化し、未承認アクセスや異常なトラフィックパターンを迅速に検出するシステムを導入する必要があります。これにより、潜在的なサイバー攻撃を早期に発見し、対策を講じることが可能です。
セキュリティ対策の段階的適用
古いシステムや運用中の設備に対しては、OSのアップデートやパッチ適用を段階的に進め、セキュリティリスクの軽減を図る必要があります。また、ウイルス対策ソフトや次世代の脆弱性検知ツールの導入も検討すべきです。
ITとOTの連携
OTネットワークの管理には、ITとOTの専門知識を連携させることが不可欠です。IT部門は、OT環境特有の要件に対応しつつ、全体のセキュリティと運用効率を改善する役割を果たすべきです。
このように、IT部門がOTネットワークを効率的に管理するには、脆弱性評価、リアルタイム監視、ITとOTの連携が重要な要素となります。IT部門が担うべき役割は拡大しており、適切なツールと手法を駆使してOTの安全と効率性を保つことが求められています。
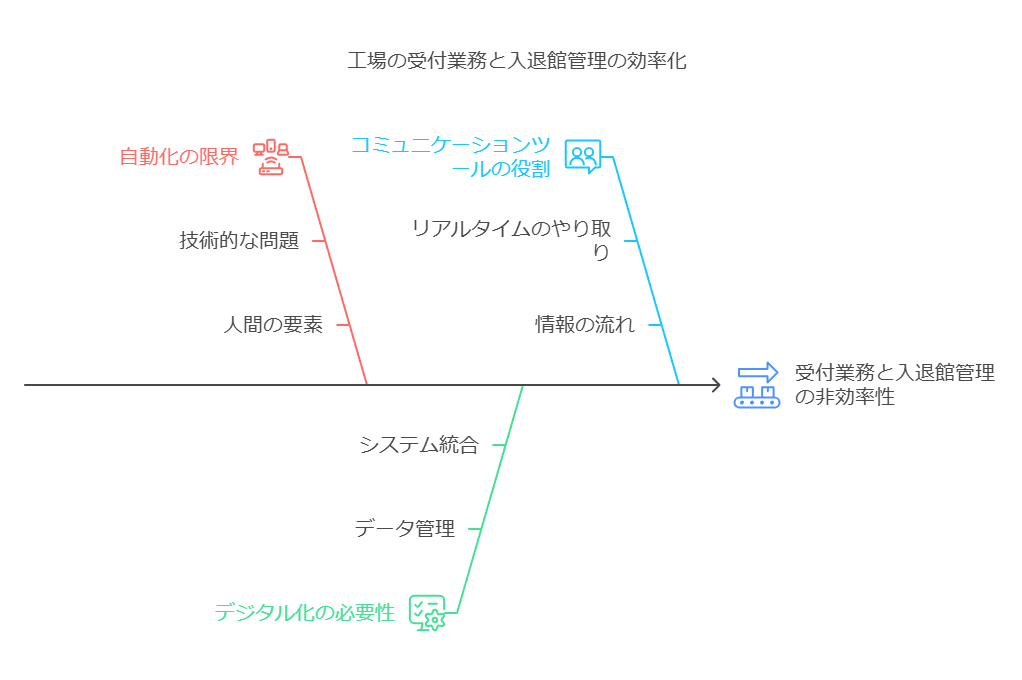
現状把握を明確化(データの視点で問題を整理)
特に重視されている監視対象のネットワーク機器は、オフィスや店舗といったリモート環境での正常な稼働を担保するネットワーク機器であることが明らかになりました。ネットワーク機器が停止すれば、サーバーやその他のビジネスインフラが停止し、企業活動が中断するリスクが高いためです。一方で、あらゆる機器の基盤である「電源」を保護するUPS(無停電電源装置)に対する監視は、全体の認識においてまだ十分ではないという結果も示されています。電源の停止は直接的にネットワーク機器の停止を引き起こし、デジタル化が進む現代のビジネスを大きく脅かす要因となります。
結果の背景とリスクを具体的に述べ、データに基づいた分析で現状を明確化
2. 問題点の明確化(データ管理とリスクの視点)
現状、多くの企業では、リモート環境にあるネットワーク機器の監視には注力しているものの、UPSに対する監視やリスク管理は不十分であり、電源保護までを含むインフラ全体のリスクに対する認識が不足しています。この認識の欠如は、企業全体のデジタル・インフラの停止リスクを高めており、今後のデータ管理やITインフラ戦略に大きな課題を残しています。
UPS監視の不足を明確にし、データとインフラ戦略におけるリスクを強調
3. 解決策の提案(データに基づく自動化と効率化の視点)
人材不足が進行する中で、インフラ全体をカバーする統合監視システムが求められます。このためには、人に依存しない自動化された監視・管理体制が必要であり、これを実現するための有効なソリューションとして、監視ソフトウェアの導入が重要です。特に、シュナイダーエレクトリックのツールは、クラウドベースの次世代データセンターインフラストラクチャマネジメント(DCIM)を提供し、データに基づくプロアクティブな管理を可能にします。
自動化と効率化に焦点を当て、データに基づいたソリューションの必要性を強調
4. ソリューションの詳細(データドリブンな価値提案)
シュナイダーエレクトリックの共通IoTフレームワークを活用し、遠隔のマルチサイト環境におけるリアルタイムの監視とデータ分析を可能にします。これにより、従来のDCIMが提供していたIT資産管理や環境監視に加え、複数の拠点にわたるネットワークの監視、リスク分析、キャパシティ管理、メンテナンス支援、さらには将来のインフラ設計まで一貫したサポートが可能となります。企業が持つ膨大なデータを活用し、プロアクティブなリスク管理と効率的なインフラ運用を実現します。
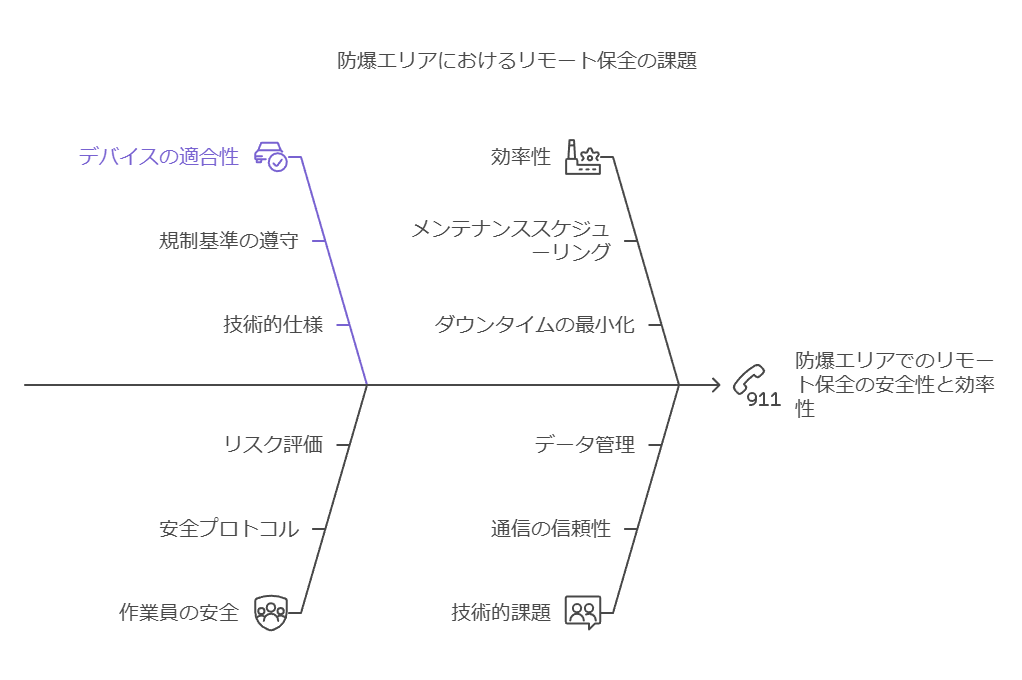
企業のネットワーク環境は従来、社外との通信をゲートウェイで制御し、外部からの脅威を防ぐことが主流でした。このアプローチにより、ゲートウェイのセキュリティ強化が企業全体の防御力向上につながっていました。しかし、近年のクラウドサービスの普及やモバイルデバイス、Wi-Fi、IoTの進展により、この前提は大きく変化しています。
クラウドサービスは基幹システムさえもサービスとして提供されるまでに拡大し、日本政府によるISMAP(政府情報システムのためのセキュリティ評価制度)もこれを支援しています。このようなサービスは、デバイスや場所を問わずアクセスが可能であるため、従来の「社内外」というネットワーク境界の概念はもはや通用しません。
モバイルデバイスの高性能化も進み、特にタブレット端末は大画面で高速処理が可能となり、クラウドアプリケーションの活用により、どこでもノートパソコンと同等の業務が行えます。さらに、多くのデバイスには標準でVPNが搭載され、VDIやリモートアクセスを通じて社内システムへの接続も容易になっています。
Wi-Fiの普及も企業のネットワークセキュリティに新たな課題をもたらしています。モバイルデバイスはほぼすべてWi-Fi対応となり、屋外でも広範に利用可能です。これにより、従業員は企業ネットワークに接続せずに、直接インターネットへアクセスできる機会が増え、企業のセキュリティポリシーの再考が求められます。
また、IoTの急速な普及とそれに伴うサイバーリスクも無視できません。従来はネットワークに接続されていなかった機器がIoT化されることで、新たな攻撃の標的となるケースが増加しています。例えば、家庭用のブルーレイレコーダーや外付けハードディスク、プリンタなどのIoTマルウェアに感染し、大規模なDDoS攻撃の踏み台にされる事例が報告されています。
このような変化を踏まえ、企業は従来の境界型セキュリティに加え、クラウドやモバイル、IoTに対応した新しいセキュリティ戦略の構築が急務です。企業ネットワークの分離が難しくなる一方で、統合的かつ包括的なセキュリティアプローチが求められています。