目次
工場IoT市場の成長とデータ活用による競争力強化
工場IoT市場は2020年から2025年にかけて、3倍の成長が予測されています。この成長は、製造業のDX(デジタルトランスフォーメーション)の加速に伴い、工場現場での「見える化」ニーズが急増していることが背景にあります。以下のようなIoT導入によるメリットが、企業の競争力向上や持続可能な経営に大きく寄与しています。
設備状態のモニタリング: 機器の不調や不具合を事前に検出し、予防保全の実現をサポートします。
遠隔監視・自動化: 人件費やメンテナンスコストの削減を実現し、効率的な運用を促進します。
品質管理の向上: 製品の品質向上や不良品の削減が可能となり、顧客満足度の向上に寄与します。
ビッグデータ活用: 将来の需要予測に基づいた生産計画を立てることで、在庫コストの削減や生産効率の向上を実現します。
エネルギー管理: エネルギー消費データを収集・分析することで、エネルギー効率の最適化やコスト削減が可能となります。
これらのIoT技術の導入により、工場全体の運用効率を向上させるだけでなく、環境負荷の軽減や持続可能な成長の実現を支援します。
急増するIoTデバイスと一元管理の重要性
一方、工場内でのIoTデバイスの増加により、運用管理における課題が顕在化しています。センサーやアクチュエーターの急増に伴い、以下のような問題が発生しています。
配線の複雑化: ケーブルの増加により、設置やメンテナンスの難易度が上がり、配線管理が困難になります。
スペースとケーブル管理の課題: 配線スペースの確保やケーブルの物理的な管理が複雑化し、不具合のリスクが高まります。
拡張の難しさ: 工場規模の拡大に伴い、ネットワークや機器の増設が進む中、全体最適化が難しくなり、スケーラビリティやシステムの負荷分散に課題が生じています。
これらの課題に対応するためには、IoTデバイスの一元管理と効率的な運用が不可欠です。
効率的な運用を実現するリモートI/Oシステムと分散制御
工場のスマート化に伴うネットワークの複雑化に対処するため、当社は「IoT時代のリモートI/Oシステム CONPROSYS nano」を用いた一元管理ソリューションを提供しています。さらに、ソフトウェアPLCによる分散制御を導入することで、次のような課題を解決します。
リモートI/Oシステムの導入に伴うコスト懸念: 構成が複雑で導入コストが高いという懸念に対しては、シンプルでコスト効率の良い構成を提案し、導入障壁を低減します。
ネットワーク拡張の柔軟性: コンパクトで手軽に増設可能な機器を提供し、スケーラブルなネットワーク拡張をサポートします。
全体最適化と負荷分散の課題: 拡張に伴う全体最適化が困難な場合でも、システムの負荷分散を考慮した構成で、最適な運用を実現します。
ここでは、工場IoT市場の成長とその背景にあるDXのニーズを強調しつつ、具体的なデータ活用のメリットと運用管理上の課題に対する解決策を明示しています。これにより、企業が競争力を高めるための具体的なステップを提供し、持続可能な成長を支援するためのアプローチを提案しています。
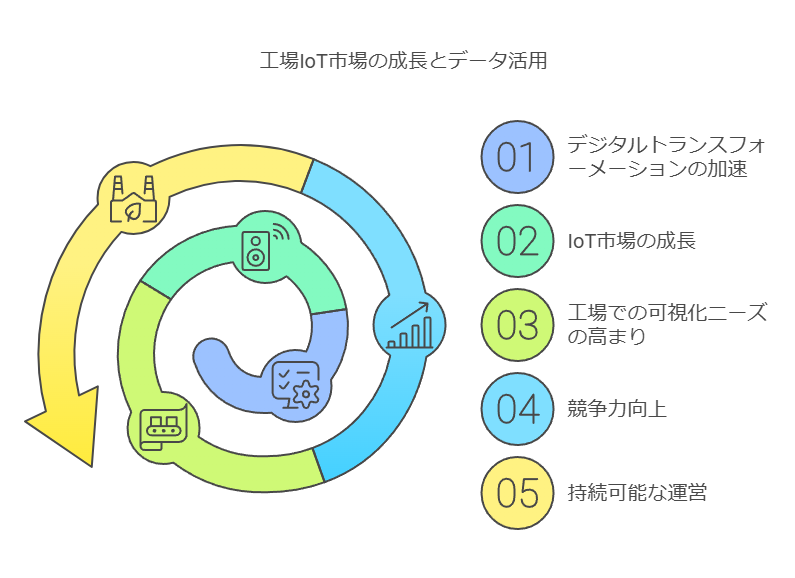
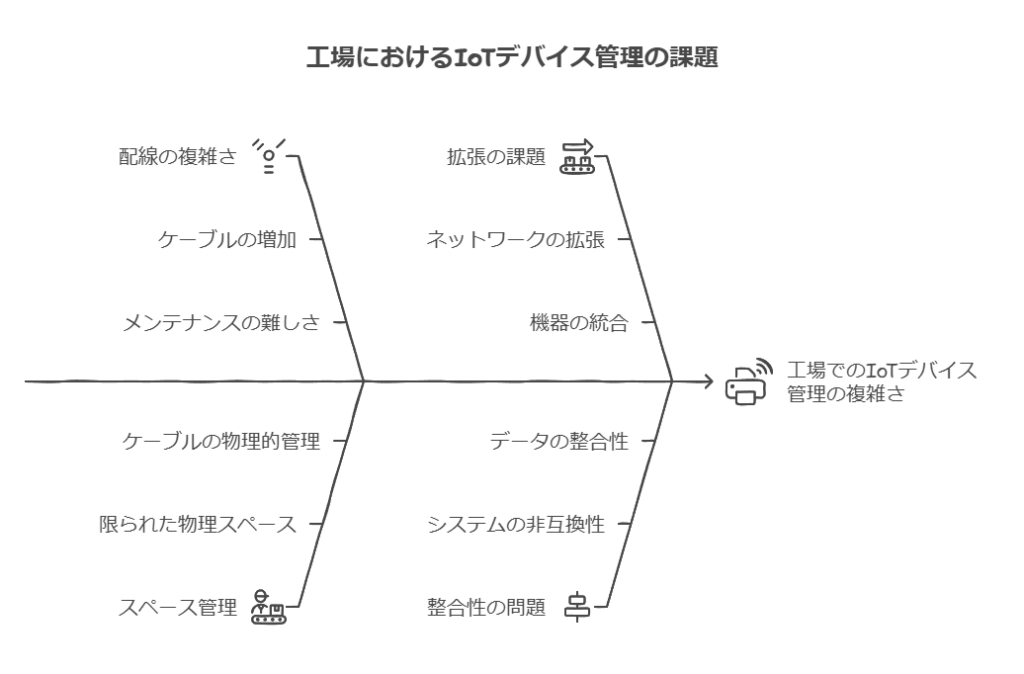
デジタル化の進展と共に高まる製造業のセキュリティリスク
近年、製造業は先進的な技術導入やIoTの普及により、デジタル化の波に乗りつつあります。しかし、その一方で、セキュリティ脅威も急速に高まっています。具体的な脅威としては、マルウェア感染やシステム侵害が挙げられ、これらの攻撃が生産活動の遅延や、場合によっては大規模な生産停止を引き起こすリスクがあります。さらに、現代の製造業は複雑化するサプライチェーンに依存しているため、サイバー攻撃による生産停止や情報漏洩が取引先全体に波及し、甚大な影響を与える可能性が高まっています。
製造業におけるセキュリティ対策の難題
製造業のセキュリティ対策には、多くの独自の課題が存在します。製造業のDX(デジタルトランスフォーメーション)が進展する中、以前は孤立していたIoTやOT環境が、ネットワーク接続されるケースが増加しています。これらの環境は、一般的なITシステムとは異なる独自のネットワーク技術やプロトコルを使用しており、セキュリティ対策の適用が一筋縄ではいかないことが多いです。さらに、古い技術が使われていることも少なくなく、最新のセキュリティ対策を適用することが困難な場合もあります。
これに対し、製造業では、従来のIT環境におけるセキュリティ対策であるアップデート管理、エンドポイント保護、リアルタイムモニタリングに加え、IoT/OT環境に特有の旧新技術が混在する状況に対しても、脆弱性の可視化とリスク対応を行うことが不可欠です。効果的な対策を講じることで、セキュリティリスクを最小限に抑え、生産活動の安定性を確保することが求められます。
製造業が直面する課題
製造業は少子高齢化の進行により、社会全体での労働力不足に直面しています。これに加え、コロナ禍や世界情勢の変化により資材確保の困難さが増し、人件費の高騰など、製造業界は多くの課題を抱えています。このような複雑で厳しい環境の中で、製造業が競争力を維持し続けるためには、セキュリティ強化を含めた全体的なデジタル戦略の見直しと最適化が不可欠です。
ここでは、データコンサルタントとして、セキュリティリスクの評価と対策の重要性を強調しています。特に製造業に特有の課題を取り上げ、DX推進におけるセキュリティ戦略の見直しが必要であることを示唆しています。また、労働力不足や資材調達の難しさなど、製造業が直面する広範な課題に対して、包括的なアプローチが求められることを提案しています。
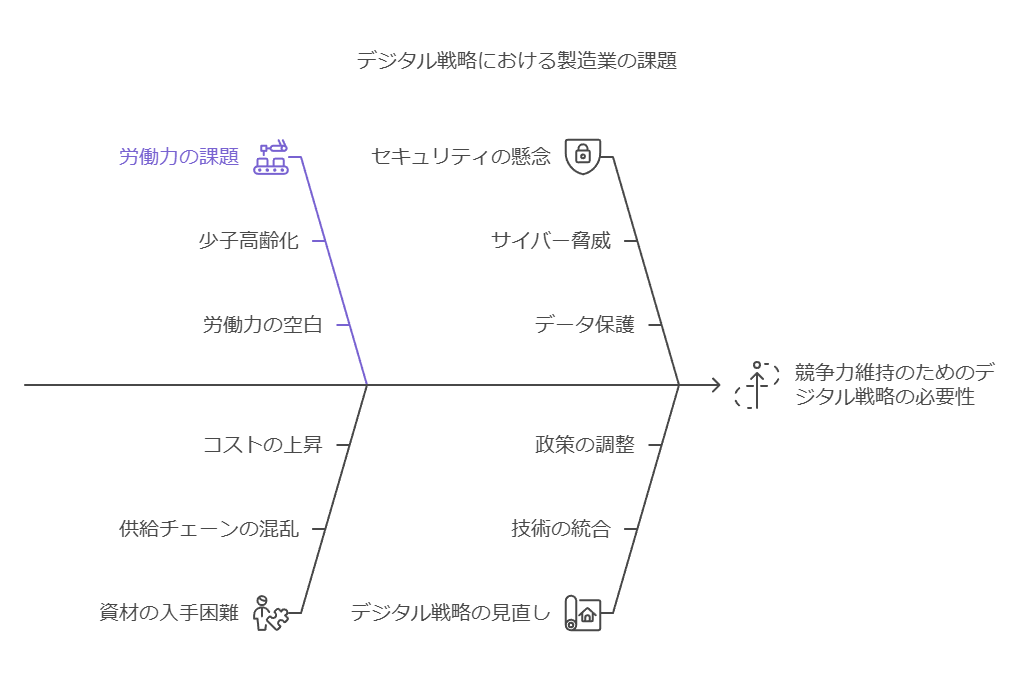
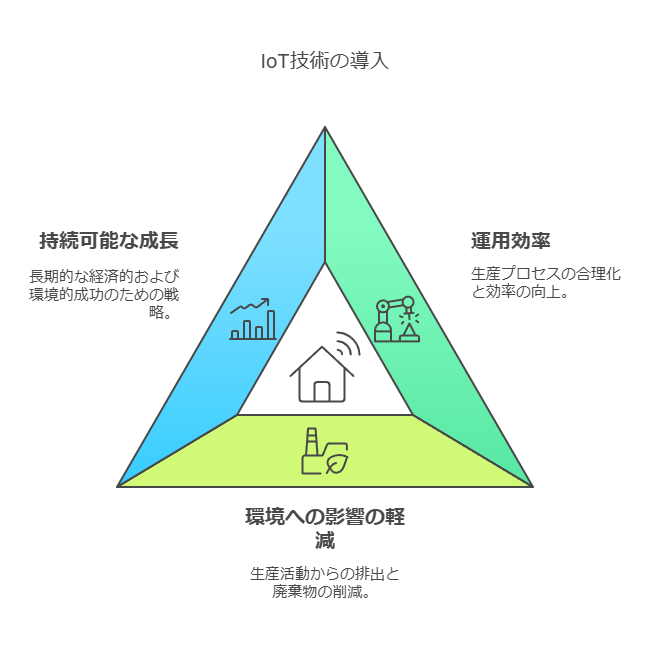
製造業における部品構成の複雑化とその影響
近年、製造業界では技術の進化、顧客ニーズの多様化、そして各国の規制強化など、多岐にわたる要因が影響し、製品の部品構成が複雑化しています。さらに、サプライチェーンの複雑化や半導体不足、原材料の価格高騰といった外部要因が、部品の入れ替えや価格改定を頻繁に引き起こしています。
こうした状況下では、機会損失を防ぎ、顧客との信頼関係を強化するために、最新の製品状況を正確に反映した部品構成と価格を迅速に提示できる体制が不可欠です。しかし、特に受注仕様生産(CTO)や受注生産方式(BTO)を採用している企業では、これを実現するための見積作成プロセスが複雑化し、作業負荷が増大しています。
見積作成の課題と顧客要求への対応
部品構成が複雑な製品に対して、営業担当者は以下の点を確認する必要があります:
顧客要件を満たすオプションの確認: 顧客の要求に沿った最適なオプションを選定し、提案すること。
部品の組み合わせの精査: 適切な部品の組み合わせを行い、構成ミスを防ぐこと。
納期や供給リスクの確認: 納期が長い部品や終息した部品の有無を把握し、リスクを最小限に抑えること。
これらを正確に行うためには、最新の部品データに基づいた詳細な確認が必要であり、営業部門と設計部署などの専門部署との密接な協力が不可欠です。場合によっては、顧客要件の正確な理解を深めるために、社内の専門家が商談に同席することも求められます。このようなプロセスは、見積作成に数週間から1か月近くかかるケースもあり、生産性の向上とスピーディーな対応が課題となっています。
BTO/CTO製造業向けの見積作成時間を大幅に短縮するソリューション
これらの課題を解決し、見積作成プロセスを効率化するためのツールを導入することで、BTO/CTO製造業における見積作成時間を最大96%短縮する具体的な方法が存在します。
このソリューションは、以下の特長を備えたサービスプラットフォームです:
製品構成から価格設定、見積作成までを一元化: 製品の複雑な構成にも対応し、CRMやERPなど他システムとのシームレスな連携が可能です。
ローコード開発対応: ITの専門知識がなくても、構成の修正や運用が容易に行えます。
リアルタイムでの見積作成: 営業担当者は、複雑な製品構成でも正確な見積を迅速に作成でき、顧客へのレスポンスを大幅に向上させることができます。
このソリューションは、以下のような課題を抱える方に最適です:
専門家の確認なしには見積作成が困難な状況にある方
顧客への見積提出が遅延し、ビジネスチャンスを逃している方
見積ミスや構成変更による手戻りが頻発している方
ここでは、製造業における部品構成の複雑化とそれに伴う課題を明確にし、データを活用した効率化ソリューションを提案しています。企業が直面する具体的な問題に対して、実践的な解決策を提示することで、データコンサルタントとしての視点を強調しました。

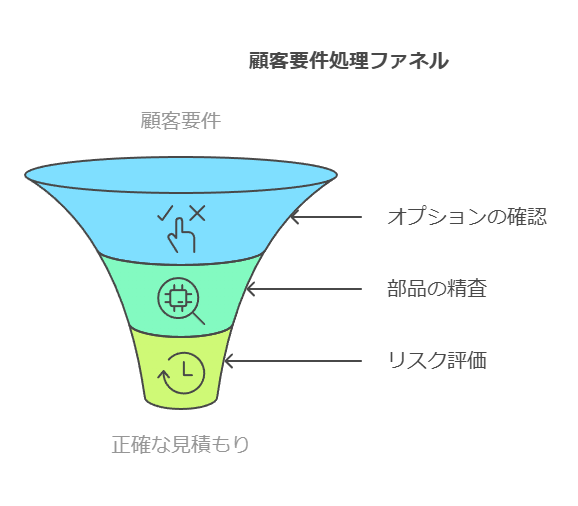
製造業DX推進とICT戦略立案に向けた指針
製造業のDX(デジタルトランスフォーメーション)が急速に進む中、工場IoT市場は2020年から2025年にかけて3倍の成長が予測されています。この変化の中で、DX推進やICT戦略の立案に携わる方々、そして業務効率化と技術伝承に課題を抱える企業にとって、現場の見える化が重要なテーマとなっています。
工場IoTによる競争力向上と持続可能な経営の実現
工場におけるIoTの導入は、企業に多くの利点をもたらします。例えば:
設備のモニタリングと予兆検出:リアルタイムで機器の状態や稼働状況を把握し、不調や不具合の予兆を早期に検出することで、ダウンタイムを最小限に抑えます。
遠隔監視と自動化:人件費やメンテナンスコストを削減し、効率的なオペレーションを実現します。
品質管理の強化:品質データの集約と分析により、製品の品質向上や不良品の削減が可能になります。
ビッグデータによる需要予測:収集されたデータを活用して、将来の需要を予測し、供給計画を最適化します。
エネルギー消費の管理:エネルギー消費データの分析を通じて、コスト削減と環境負荷の低減を目指します。
これらの取り組みは、企業の競争力向上と持続可能な経営に大きく寄与します。
増加するIoTデバイスと運用課題の克服
一方で、工場内のIoTデバイスの増加に伴い、運用面での課題も顕在化しています。具体的には:
配線の複雑化:増加するケーブルにより、配線が複雑化し、設置やメンテナンスの難易度が上昇します。
管理の難易度:スペースの確保やケーブルの把握が難しくなり、不具合のリスクが増大します。
拡大する規模への対応:工場規模の拡大に伴い、機器やネットワークの管理が複雑化し、全体最適な構成の実現が難しくなります。
これらの課題に対応するためには、効率的な運用と管理が求められます。
効率的な運用のための技術的アプローチ
工場のスマート化に伴う現場ネットワークの複雑化に対応するため、以下のような手法が有効です:
リモートI/Oシステム:センサーやアクチュエーターを分散配置し、配線の複雑化を軽減します。
ソフトウェアPLCによる分散制御:工場内の制御を分散化し、柔軟で効率的なオペレーションを実現します。
これらの具体的な手法を取り入れることで、現場の運用効率を向上させ、DX推進におけるICT戦略の成功を支援します。
ここでは、データコンサルタントの視点から、製造業におけるDX推進のための具体的な戦略と技術的なアプローチを強調し、効率的な運用と管理の重要性を明確にしています。
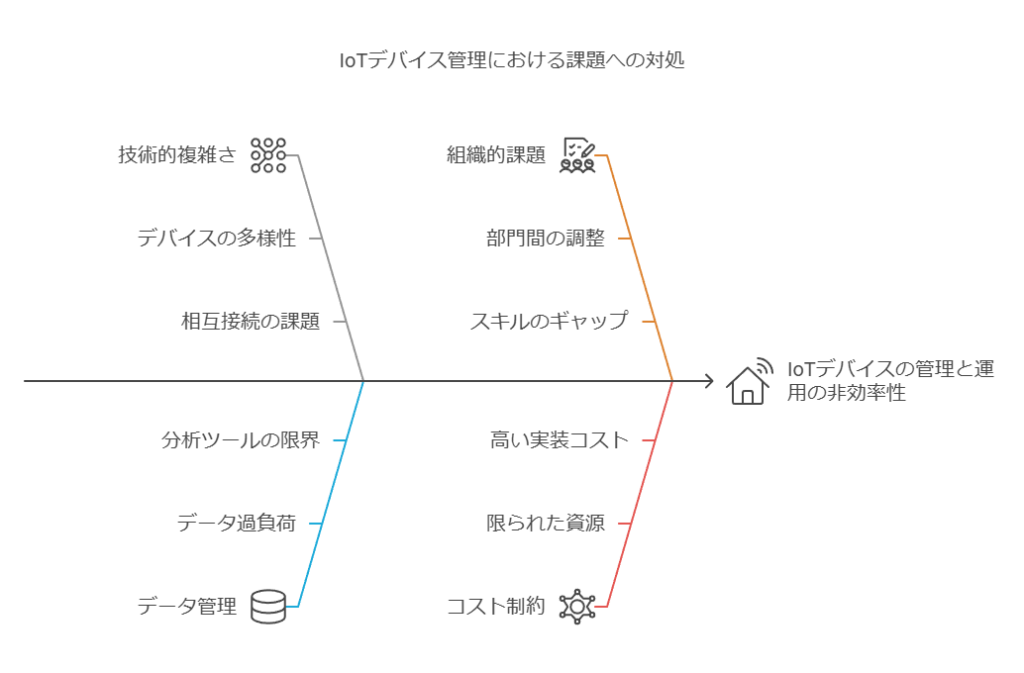
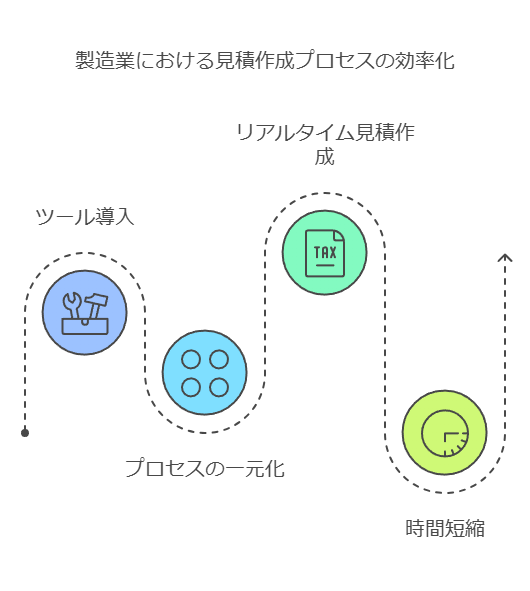
1. 在庫管理の適正化が求められる理由
在庫管理の複雑化と企業が直面する課題
多品種少量生産への移行が進む中、企業は多くの取引先との関係を構築し、それに伴い製品の種類も増加しています。この結果、在庫管理が一層複雑化し、正確な需要予測が難しくなっています。多くの企業は、この不確実性に対応するために安全在庫を増やしていますが、在庫の増加にはリスクが伴います。具体的には、在庫が過剰になると倉庫コストの上昇や在庫の陳腐化リスクが生じるだけでなく、キャッシュフローの悪化にもつながる可能性があります。
2. リスクに対するバランスの取れた在庫管理
在庫不足がもたらす潜在的なリスク
一方で、在庫を極端に減らすことにもリスクがあります。自然災害やパンデミック、さらにはサイバー攻撃といった予測不可能なセキュリティインシデントにより、仕入先からの納品が滞ると、製造の継続が困難になることがあります。こうしたリスクを回避するため、必要最小限の在庫を確保することが求められますが、そのためには市場の変化に柔軟に対応できる在庫管理の仕組みが不可欠です。
3. 市場の変化に対応した在庫管理の適正化
生産コスト削減とキャッシュフロー改善のための適正在庫管理
市場の需要に柔軟に対応しつつ、生産コストの削減とキャッシュフローの改善を実現するためには、適正な在庫数を常に把握できる仕組みが必要です。これには、リアルタイムでの需要予測やサプライチェーン全体の可視化を支援するデータ分析ツールの導入が効果的です。データ駆動型の在庫管理戦略を取り入れることで、企業は在庫の過不足を最適化し、持続可能な生産活動を維持することができます。
4. 製造業における多品種少量生産へのシフト
グローバル化と消費者ニーズの変化に対応する製造戦略
近年、製造業はグローバル化の進展や消費者ニーズの多様化、サプライチェーンの最適化など、複雑な事業環境に直面しています。消費者の要求が細分化され、製品のライフサイクルが短縮される中、企業は市場の変化に迅速かつ柔軟に対応する必要があります。このため、多品種少量生産へのシフトが加速しており、これを支えるための高度な在庫管理戦略の重要性が増しています。
5. データ駆動型在庫管理の導入による競争力強化
データ分析を活用した在庫管理の最適化
データ分析を活用した在庫管理の導入は、企業が競争力を維持し、変化する市場環境に対応するための鍵となります。リアルタイムデータを活用し、需要予測の精度を高めることで、在庫の過剰や不足を防ぎ、効率的な生産活動を実現します。また、適切なデータ統合と分析により、サプライチェーン全体の可視性が向上し、意思決定の迅速化が可能になります。これにより、企業は持続的な成長と収益性の向上を達成することができます。
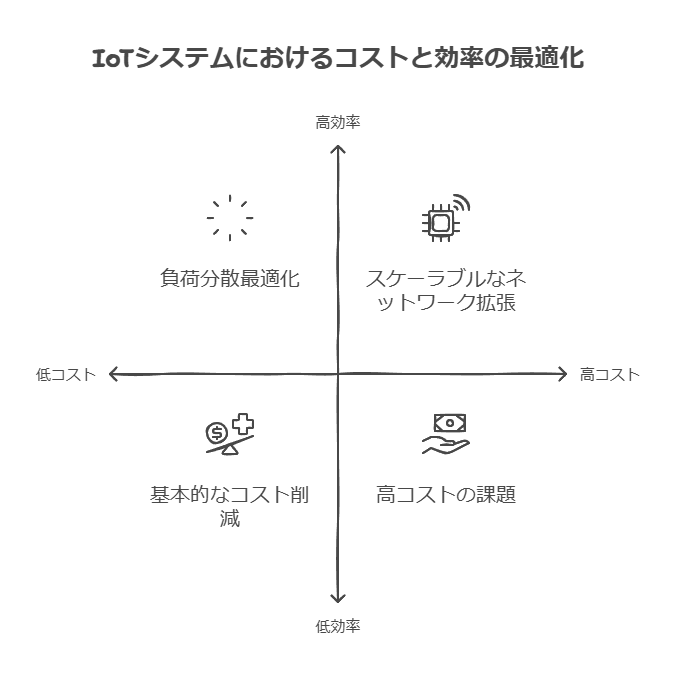
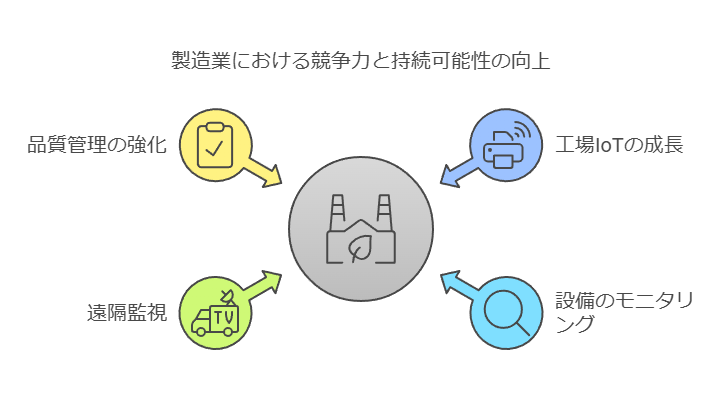
OT資産管理におけるサイバーセキュリティの課題と対応策
近年、OT(Operational Technology)資産に対するサイバー攻撃が増加しており、各種資産の脆弱性を管理することが喫緊の課題となっています。しかし、実際にOT資産の管理を行う際、どのようなツールを導入し、どのように効果的な運用を行うべきか、具体的なイメージを持ちにくい担当者も少なくありません。
OT資産管理とリスク管理の実践手法
OT資産管理においては、以下の点を重点的に考慮する必要があります:
平時の状態を把握する: 正常な運用状態を常に把握しておくことで、異常の早期発見が可能になります。これはリスク管理の基本であり、平時の状態を把握するためのツールの導入が推奨されます。
異常状態の発見: リアルタイムで異常を検知し、迅速な対応が可能な体制を整えることが重要です。これには、AIを活用した異常検知システムの導入が効果的です。
日々の運用最適化: 日々の運用をスムーズに進めるためには、具体的な事例やデモを参考にし、効果的な運用プロセスを確立することが求められます。
製造業における多様なセキュリティリスクへの対応
製造業では、外部からのサイバー攻撃に加えて、内部関係者による技術情報の不正持ち出しといったセキュリティリスクも増加しています。IPAが2023年1月に発表した「情報セキュリティ10大脅威」では、「内部不正による情報漏えい」が4位にランクインしており、これに対する対策が急務です。
これらのリスクに対して、以下の対応策が有効です:
内部監視体制の強化: 社内のアクセス権限管理やログ監視を強化し、内部からの不正行為を未然に防ぐことが求められます。
教育と意識向上: 従業員のセキュリティ意識を高め、内部不正のリスクを軽減するための教育プログラムを導入することが効果的です。
IoT時代の「エッジコンピューティング」と「コンテナ技術」の台頭
製造業のデジタル化が進む中で、オンプレミス環境とクラウド環境を組み合わせたハイブリッドなシステムインフラが主流となりつつあります。その中でも特に注目されているのが、「エッジコンピューティング」の導入です。
エッジコンピューティングの利点: 大量のデータをリアルタイムで処理する能力が求められる製造現場では、エッジコンピューティングを活用することで、データの即時分析が可能となり、現場の効率化が進みます。
コンテナ技術の採用: エッジ側でのアプリケーション展開には、コンテナ技術が有効です。コンテナ技術は、高速で効率的なデプロイが可能で、エッジコンピューティング環境においても柔軟なシステム運用を実現します。
ここでは、OT資産管理におけるサイバーセキュリティの重要性と、その具体的な対応策を明確にしました。また、製造業における多様なセキュリティリスクへの対応や、IoT時代のエッジコンピューティングとコンテナ技術の利点を強調し、実践的なアプローチを提案しています。
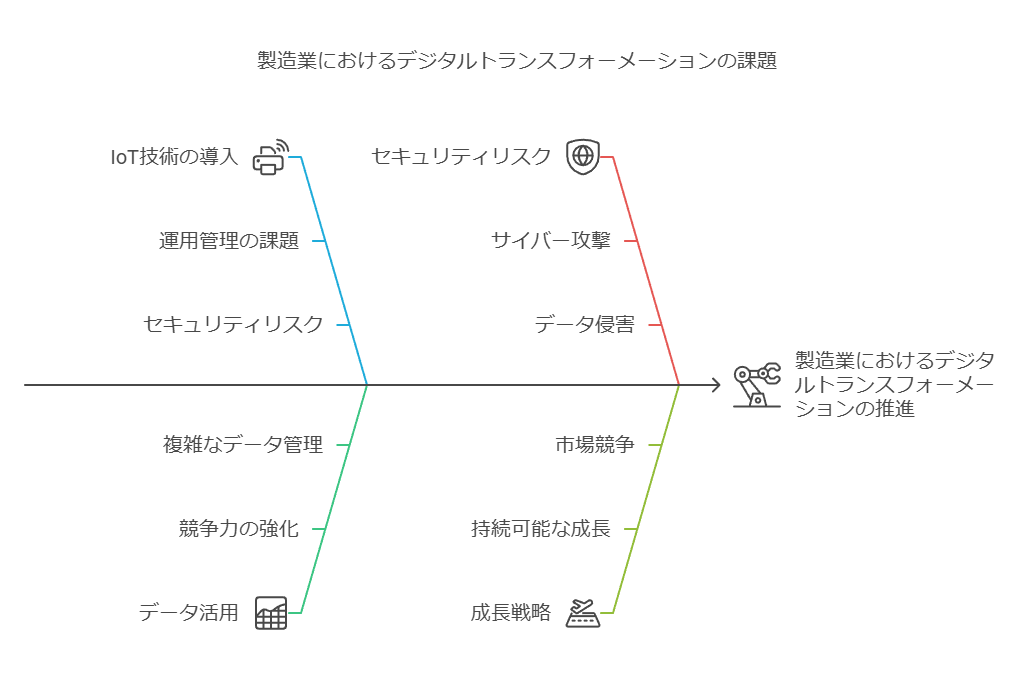
「産業IoTセキュアリモートマネジメント(SRM)」によるスマートファクトリ化の実現
工場から収集される多種多様なデータを「産業IoTセキュアリモートマネジメント(SRM)」を通じて各アプリケーションに連携することで、IoTデータの可視化と分析を行い、さらに製造業における各基幹システムの統合をサポートします。これにより、スマートファクトリ化をワンストップで推進するソリューションをご提案します。
デジタル化の重要性:作業指示書、チェックリスト、マニュアル
製造業における作業指示書、チェックリスト、マニュアルなどの文書のデジタル化は、作業効率の向上、技術伝承の促進、そしてコンプライアンス対応の観点から急務となっています。紙ベースの管理から脱却し、データによる管理体制への移行は、今や不可欠な要件となっています。
真のデジタル化とは:業務効率化とノウハウ伝承の実現
単に紙の文書を電子化するだけでは、業務効率化やノウハウ伝承といった根本的な課題の解決にはつながりません。デジタル化の真の利点を引き出すためには、定常作業や非定常作業を問わず、状況に応じて柔軟に対応できる作業フローを構築し、リアルタイムデータに基づく業務改善を図る必要があります。
迷わず作業できるフローの構築:デジタル化文書の活用
デジタル化された文書を効果的に連携させ、誰でも迷わず作業が進められる最適なフローを構築するための方法について解説します。このプロセスを通じて、作業フローの最適化とノウハウ伝承の強化を同時に実現するソリューションとして、「XperteyeProceed」をご紹介します。
DXの成功を支える構想、導入、運用の一貫サポート
デジタルソリューションの導入は、DXの成功を約束するものではありません。DXを現場で実際に効果的に実現するためには、単なるツールの導入にとどまらず、パートナー企業である株式会社アウトソーシングテクノロジーの支援を受け、課題の洗い出しから運用までを一貫してサポートすることが不可欠です。この包括的な支援体制により、DXの効果を最大限に引き出し、現場の生産性と効率を向上させることが可能です。
ここでは、データコンサルタントとして、製造業におけるデジタル化の重要性を強調し、スマートファクトリ化を推進する具体的なソリューションを提案しました。また、DXの成功には、デジタルツールの導入だけでなく、構想から運用までの一貫したサポートが重要であることを強調しました。
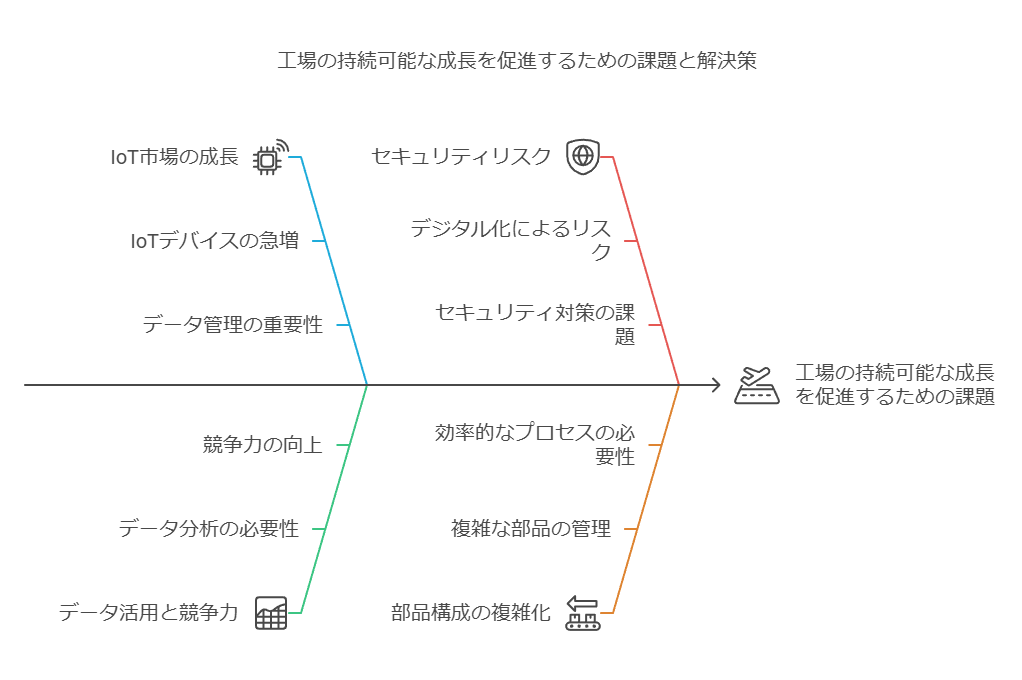
複雑なリモートI/Oシステム導入とネットワーク拡張の課題解決
多くの製造業が直面している以下の課題に対して、データコンサルタントとしての視点から、最適な解決策を提案します。
リモートI/Oシステムの導入に伴う懸念: 複雑な構成や高コストが懸念されていますが、適切なアーキテクチャの設計とスケーラブルなソリューションの導入により、コストを抑えつつ効果的なシステムを実現できます。
ネットワーク拡張のニーズ: コンパクトで手軽に増設可能な機器を探している企業には、モジュラー型のネットワークソリューションが適しています。これにより、段階的な拡張と柔軟なスケーラビリティを実現します。
全体最適とシステム負荷分散の課題: 拡張後のシステムで全体最適が図れていない企業には、負荷分散の最適化やシステムの統合管理を支援するプラットフォームの導入が有効です。これにより、スケーラビリティとパフォーマンスを両立させることが可能です。
経営管理システムの進化による経営判断の支援
従来の生産管理を主体とした経営管理システムは、各領域の情報が分散し、経営者が正確な情報をタイムリーに取得できない環境を生んでいます。さらに、COVID-19や部品費の高騰、サプライチェーンの断絶など外部環境の不透明さが増す中で、経営判断の複雑さが増しています。
課題を克服するための提案:
新しい経営管理システムへの移行: これにより、経営者がリアルタイムで正確な情報にアクセスし、迅速かつ的確な意思決定を行える環境を構築します。新システムは情報の統合と可視化を強化し、外部環境の変化に迅速に対応できる柔軟性を提供します。
IT人材不足がもたらす運用負担とクラウドソリューションのメリット
現場では、生産管理システムのバージョン更新やセキュリティ管理がIT人材の不足によって大きな負担となっています。この問題を解決するために、クラウドネイティブな環境の導入が鍵となります。
クラウド型(SaaS)ソリューションの利点:
運用管理の効率化: ソフトウェアの更新作業やバージョン管理、セキュリティ管理などの手間を大幅に削減します。これにより、現場の負担が軽減され、ITリソースを他の重要業務に集中させることができます。
生産管理・経営管理システムの選定ガイド: これからのシステム選びでは、クラウド型ソリューションの柔軟性と自動化機能を重視することが重要です。これにより、長期的な運用コストの削減とシステムの拡張性を確保できます。
成功事例の紹介: 経営管理システムの変革とその成果
ある製造業が新しい経営管理システムに置き換えた際の具体的な事例を紹介します。この事例では、変革過程での課題と、システム移行後に得られた成果を詳述します。
変革のプロセス: 課題の特定からソリューション選定、実装に至るまでのプロセスを詳細に解説し、現場のニーズに即した変革をどのように進めたかを説明します。
成果と効果: システム移行後の効果として、業務効率の向上、意思決定の迅速化、そして全体的なコスト削減を達成した点を強調します。
ここでは、データコンサルタントとしての視点から、製造業の課題に対する解決策を具体的かつ実践的に提案し、現場の負担軽減と経営判断の質向上を支援する内容に変更しました。
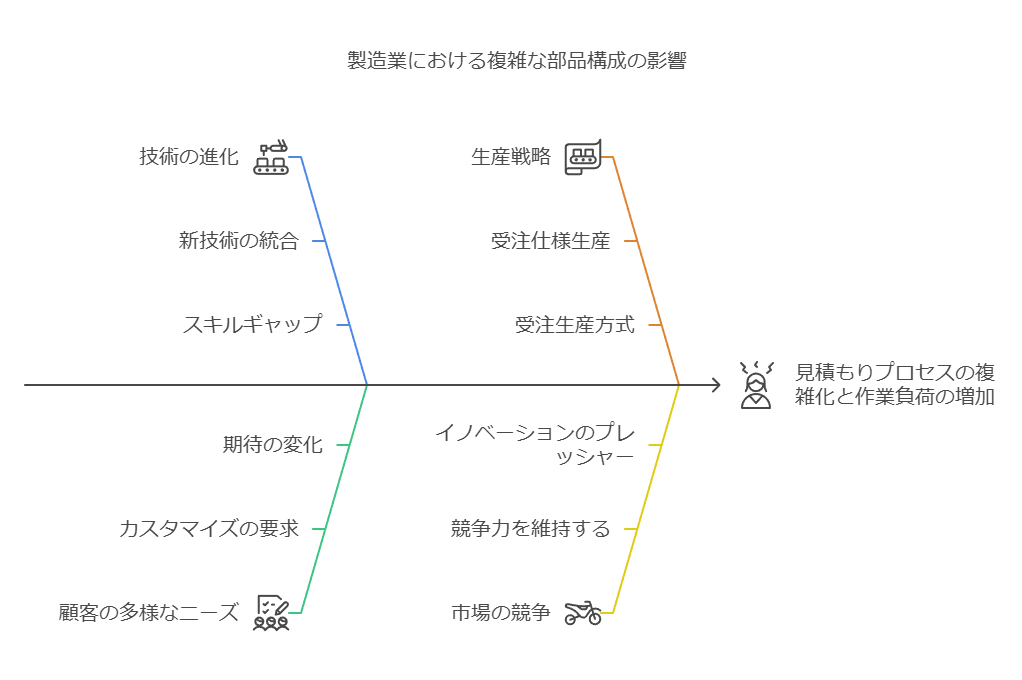
製造業におけるデータ活用の加速
各業界でDX(デジタルトランスフォーメーション)が進展する中、製造業でもデータ活用が急速に進んでいます。製造部門だけでなく、調達、物流、研究開発、販売、営業、マーケティング、経営企画、財務など、全ての業務領域でデータが活用され、業務改善や新たな価値創造に寄与しています。
データのサイロ化による情報格差の課題
しかし、各業務領域でのデータ活用が進む一方で、オペレーションのサイロ化が進み、「部分最適」に留まるケースが散見されます。この結果、現場と経営層の間で情報の認識に齟齬が生じたり、部門間での認識のズレにより、データ連携が進まず、オペレーションが効率的に行われていないといった課題が発生しています。
「部分最適」の限界
日本の製造業は、オペレーショナル・エクセレンス(Operational Excellence)として世界的に高く評価されています。部門ごとのデータ活用や改善活動は優れた成果を上げていますが、データが部門内に閉じたままである場合、その成果は限定的です。業務プロセス上関連する部門へのデータ共有が不足しているため、後工程が後手に回るといった事象が生じることがあります。
データ共有による「全体最適」の実現
各部門が管理する情報をタイムリーに他部門と共有することで、業務全体の効率が向上し、現場同士の意思疎通が迅速化し、よりスピード感のあるオペレーションが可能になります。また、経営層も企業全体を俯瞰した状態で状況を把握できるため、より的確なデータに基づく意思決定が可能になります。
「全体最適」を達成するための戦略
データ活用における情報格差を排除し、現場の意思決定を強化し、経営層がタイムリーに状況を把握するためには、データのサイロ化を解消し、「全体最適」を実現することが不可欠です。これを実現するためのポイントを、具体的な事例を交えながら解説します。データ活用に行き詰まりを感じている方や、さらに効果を高めたいと考えている方に向けた内容です。
このように、データのコンサルタント視点で、データ活用の課題と解決策を提示しつつ、全体最適の重要性を強調しました。
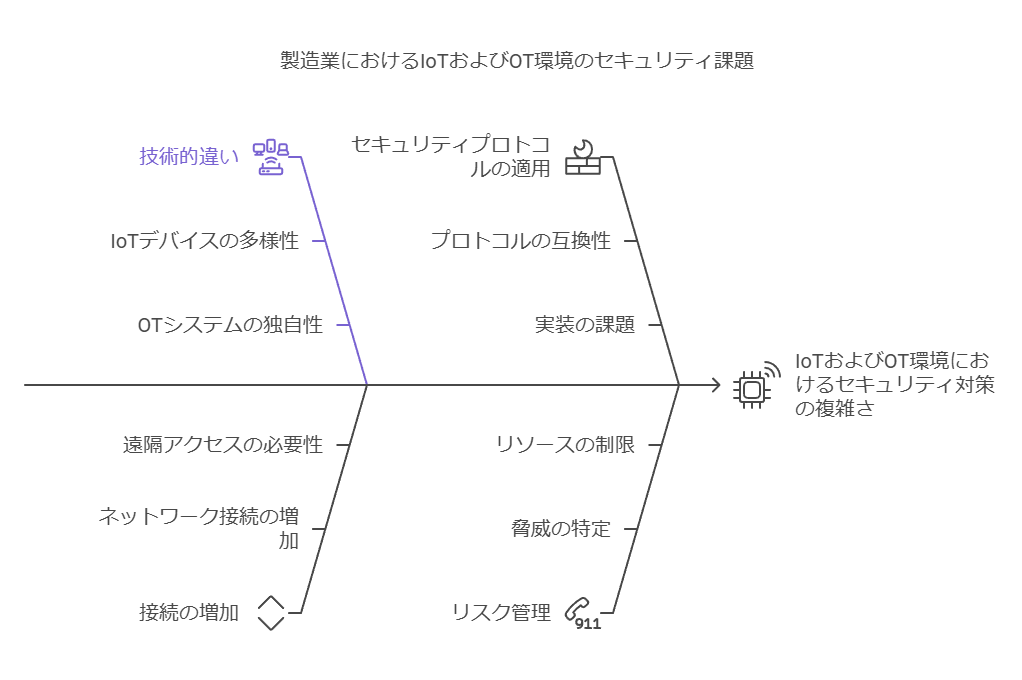
スマート工場化におけるエッジコンピューティング端末の機能要件
スマート工場の実現に向けて、エッジコンピューティング端末には以下の機能が求められます。
ハードウェアスペック: 高度なデータ処理と分析をサポートするための十分な処理能力とメモリ容量が必要です。
信頼性とサポート: 24/7の稼働を前提とした高い信頼性と、迅速なサポート対応が求められます。
耐久性: 工場環境の厳しい条件に耐えられる堅牢な設計が不可欠です。
グローバル対応: 多国籍企業における展開を考慮し、各国の規制や標準に対応する必要があります。
セキュリティ: サイバー攻撃からデータを保護するための高度なセキュリティ機能が必要です。
製造業特化アプリケーション対応: 特定の製造業向けアプリケーションやプロトコルへの対応が重要です。
AIを活用した分析機能: リアルタイムでのデータ分析をサポートするAI機能の統合が求められます。
クラウドコンピューティングとの連携: 工場データをクラウドにシームレスに連携し、広範な分析やデータ共有を可能にする必要があります。
費用対効果: 投資対効果を最大化するためのコスト効率の高いソリューションであることが求められます。
OT環境におけるデータ管理と分析のフレームワーク
スマート工場のデータ管理と分析は、以下の4つのレベルで行われます。
ライン用PC: 製造ラインに付随する機器や装置に接続され、リアルタイムのデータ収集と処理を行います。
エッジコンピューティング端末: 現場で収集されたデータを一時的に集約し、迅速なフィードバックを提供する専用端末です。
工場用サーバ: 工場全体でのデータを集約し、長期的なデータ保存と分析を行います。
クラウド領域: 工場のデータを企業全体、または企業間で連携させ、包括的な分析を容易に行える環境です。
スマート工場化におけるクラウドコンピューティングの課題
クラウドコンピューティングはスマート工場化において重要な役割を果たしますが、以下のような課題も考慮する必要があります。
セキュリティやデータプライバシーの懸念: クラウドへのデータ移行に伴うセキュリティリスクとデータプライバシーの保護が課題となります。
遅延の問題: リアルタイム処理が求められる製造環境では、クラウドへのデータ送信と応答の遅延が生産性に影響を与える可能性があります。
運用コストの問題: クラウド利用による運用コストが予算を圧迫する可能性があり、費用対効果のバランスを検討する必要があります。
自社固有の活用が難しい点: 汎用的なクラウドソリューションでは、自社特有の業務プロセスに最適化するのが難しい場合があります。
自社の及ばない所での障害発生リスク: クラウドプロバイダーの障害による影響が、自社の制御範囲を超えて発生する可能性があります。
トラブル時の責任分解が難しくなる点: クラウド環境におけるトラブル発生時、責任の所在が不明確になりがちです。
ここでは、データコンサルタントの視点から、エッジコンピューティング端末の機能要件、OT環境でのデータ管理フレームワーク、そしてクラウドコンピューティングに関する課題を明確にし、製造業におけるスマート工場化に必要な要素を網羅的に捉える内容に変更しました。
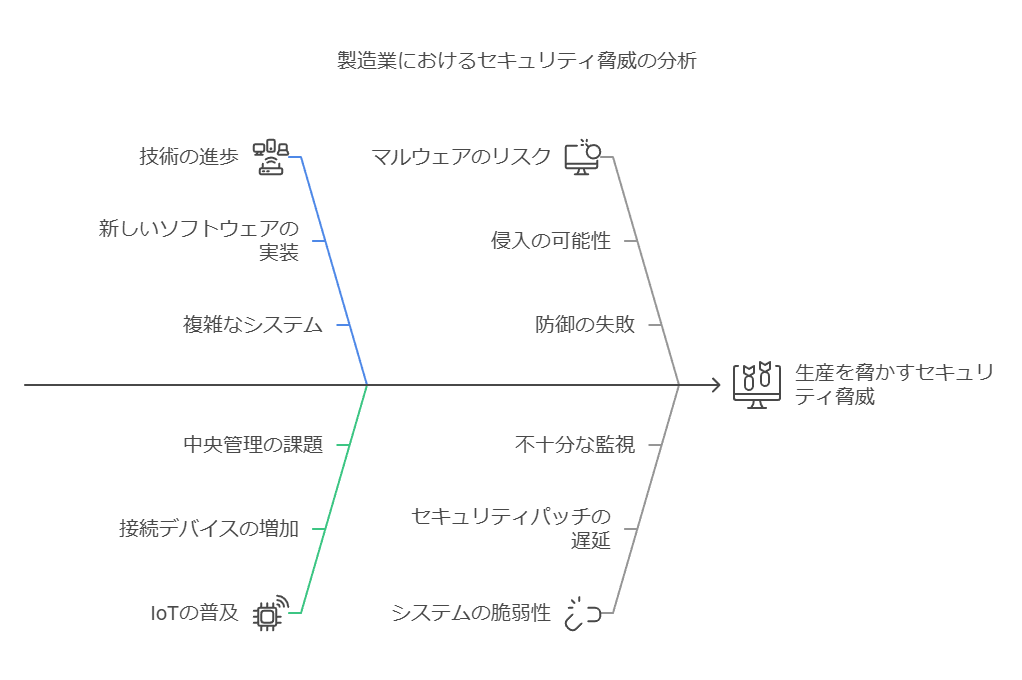