目次
1. 複雑化する生産プロセスと新たな経営課題
近年の製造業においては、消費者ニーズの多様化に伴い、少量多品種の生産、カスタマイズ、パーソナライゼーションへの需要が増加しています。これにより、製造現場では短納期と注文量の変動に迅速に対応することが求められ、生産プロセスが複雑化しています。このような状況が進む中で、効率的な生産計画を迅速に立案することが難しくなり、生産計画の属人化が顕著となっています。特に新規受注時には、短期間で正確な生産計画を立てることが困難になり、結果として現場での計画外の残業や作業ミス、品質低下、コスト増加、従業員のモチベーション低下といった経営上のリスクが発生する可能性が高まります。
2. 最適な生産計画の策定に向けた課題
製品の種類が多く、工程が複雑な製造環境では、最適な生産計画を立案するには多くの課題が存在します。まず、自社の全ての製造要件やルールを正確に理解し、それに適合するシステムを設計する必要がありますが、これは大きな初期投資と多大な労力を伴います。また、市場や技術の変化に対応し続けるためには、生産プロセスも柔軟に進化させる必要があります。これらの課題に対応するためには、固定的なシステムに頼るのではなく、柔軟かつ段階的に精度を向上させることができる生産計画システムが求められます。
3. 柔軟な生産計画システムの構築
柔軟な生産計画システムを構築するには、自社の複雑な製造要件やルールをどのように定義し、どのようにシステムに反映させるかが重要です。このプロセスでは、段階的に計画精度を向上させるためのアプローチが効果的です。たとえば、データ分析を活用して過去の生産データからパターンを抽出し、それを基にした予測モデルを構築することが考えられます。これにより、生産計画の精度を向上させ、経営リスクの低減に貢献することが可能です。
4. 経営リスクの低減と現場の効率化
柔軟な生産計画システムを導入することで、生産計画の属人化を解消し、効率的な計画立案が可能となります。特に、生産計画の精度向上や生産の見通し精度の改善に課題を感じている企業にとっては、こうしたシステムの導入が経営リスクの低減につながります。さらに、現場の生産性を向上させ、従業員のモチベーションを維持するための重要な要素となるでしょう。
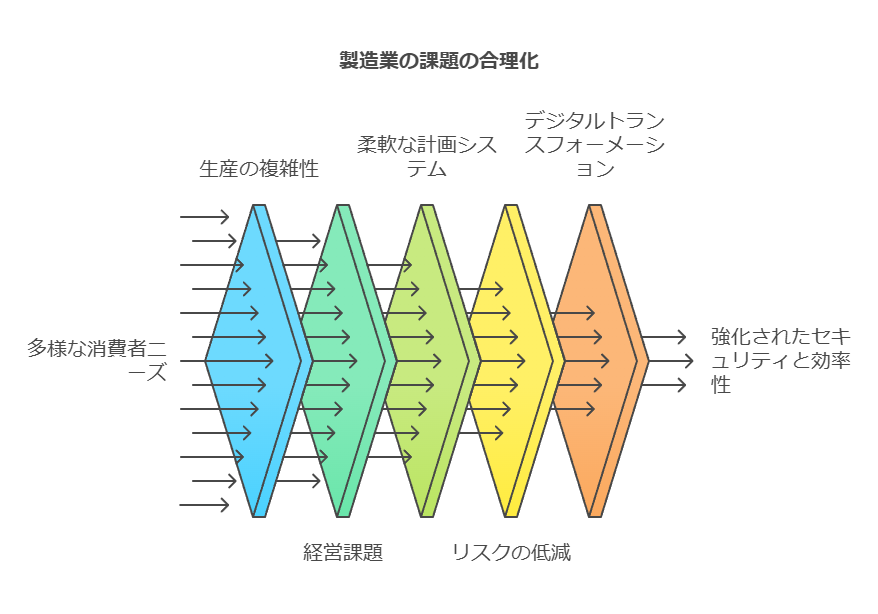
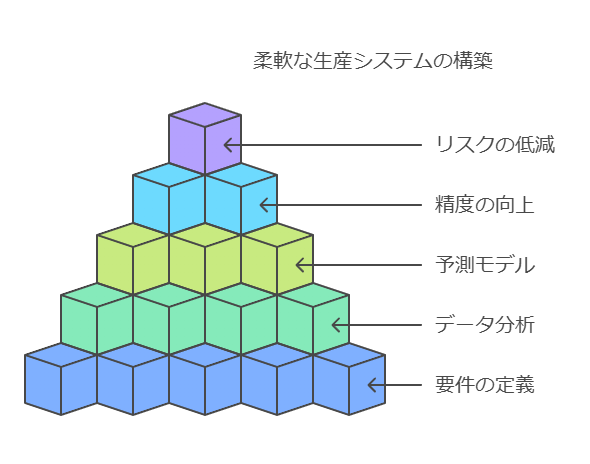
品質不正やデータ改ざんは、製造業における重大なリスクとして、2017年以降ますます顕在化しています。この問題は、特に素材メーカーを中心に広がり、企業の信頼性を大きく揺るがしています。2017年12月4日に経団連が「品質管理に係わる不適切な事案への対応について」の声明を発出したものの、品質不正やデータ改ざんは未だに多くの企業で発生しており、その背後には複数の要因が存在します。
特に需要が高まり、生産計画が厳しくなる製品において、些細なミスが生産スケジュールに影響を与え、結果的に現場での不正を誘発するリスクが高まります。業績が好調な企業ほど、品質不正を引き起こすリスクを事前に調査し、把握することが、経営にとって極めて重要です。
データ管理の脆弱性とリスク 多くの企業では、製造現場における品質データの管理が、依然として手作業に頼っています。これは、組織内の特定の個人や少数の部門に依存していることが多く、その結果として以下のような課題が発生します。
検査データが手動でPCに入力されている
検査表や成績表がExcelやAccessで作成されている
検査データが部門ごとに分散管理され、統一されていない
これらの問題は、データ改ざんのリスクを高め、組織全体の品質管理を不十分なものにし、最悪の場合、企業の存続を脅かす危機的な状況に陥る可能性があります。
品質不正を防ぐためのデジタルトランスフォーメーション(DX)の重要性 品質不正を未然に防ぐためには、データの属人化を防ぎ、情報を一元化することが不可欠です。これにより、組織全体での「品質の見える化」を実現し、リアルタイムでの監視と迅速な対応が可能となります。
データコンサルタントとして、企業が品質管理のDXを推進するためのアプローチを提案します。具体的には、以下の施策が考えられます。
データ一元化とリアルタイム監視の導入
クラウドベースのプラットフォームを活用し、検査データを一元管理することで、データの改ざんリスクを最小化します。また、リアルタイムでのデータ監視により、異常値の即時検知と対応が可能となり、品質管理の強化に繋がります。
自動化ツールの導入
手作業で行われているデータ入力や管理プロセスを自動化することで、人為的なミスを削減し、品質データの信頼性を向上させます。
データガバナンスの強化
全社的なデータガバナンス体制を構築し、データの正確性と整合性を確保します。これにより、品質データに対する透明性を高め、外部監査やコンプライアンスにも対応できる強固な基盤を作り上げます。
トレーニングと意識改革
従業員の意識改革を促し、品質管理の重要性を理解させるための教育プログラムを実施します。これにより、品質に対する責任感を高め、不正の抑止力となる社内文化を醸成します。
これらのアプローチを組み合わせることで、企業は品質不正やデータ改ざんのリスクを大幅に低減し、持続的な成長を実現するための基盤を強化することが可能です。品質管理のDXは、単なる技術導入ではなく、組織全体の信頼性と競争力を向上させるための戦略的な施策です。
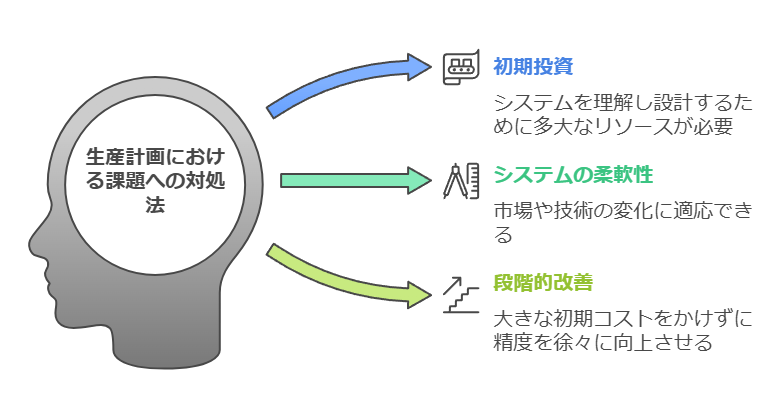
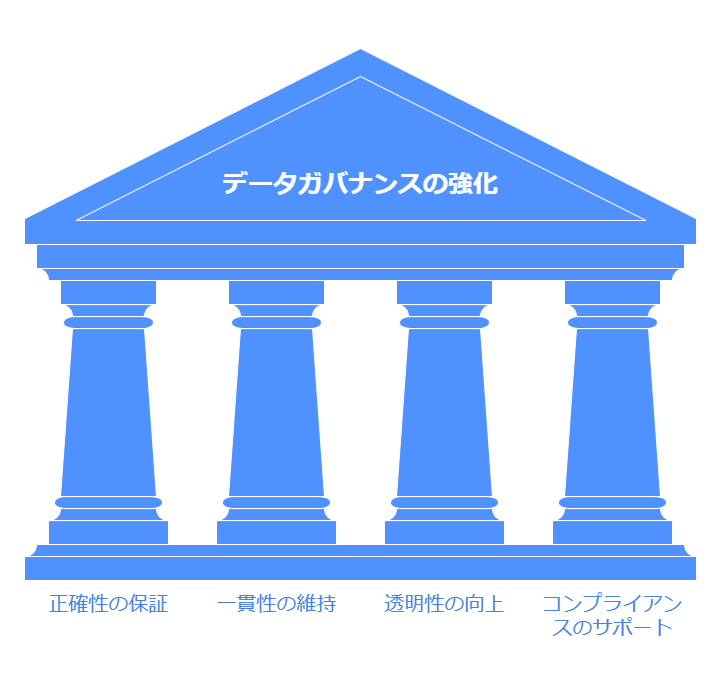
ネットワーク化を進める上で、製造業のデータ活用とセキュリティ確保の観点から、以下の技術が特に期待されています。
1. ローカル5GやWi-Fi6などの次世代ネットワーク技術
これらの技術は、工場内での高速かつ安定したデータ通信を可能にし、機器間の連携を強化します。特に、ローカル5Gは広帯域通信と低遅延を実現し、製造現場におけるリアルタイム制御やデータ収集を支えます。
2. 機器間ネットワークの標準化技術
標準化技術により、異なるメーカーの機器間でのスムーズなデータ交換が可能となり、工場全体の効率を向上させます。これにより、システム全体のインターオペラビリティが確保され、異なる機器やネットワークの規格違いを吸収して統合的なネットワークが構築されます。
3. データ連携および管理の標準化技術
データの一元管理と連携が可能になることで、データの利活用が促進されます。標準化されたデータ管理は、品質管理や生産性向上に不可欠な基盤となります。
4. リアルタイム性や信頼性を担保する「無線」通信技術
製造現場でのリアルタイム性が求められる環境において、信頼性の高い無線通信技術は、生産ラインの効率化や柔軟なレイアウト変更を可能にし、迅速な対応を支援します。
5. 低コストでネットワーク化を実現するネットワークゲートウェイ
ネットワークゲートウェイの活用により、コストを抑えつつ、簡便にネットワーク化を実現します。これにより、中小規模の製造業でも導入が進み、データ活用の拡大が期待されます。
6. 安定したセキュリティを確保する通信技術
安定した通信と高いセキュリティを兼ね備えた技術は、製造現場において非常に重要です。特に、工場向けのサイバーセキュリティ技術の導入は、外部からの攻撃や内部不正の両方に対して効果的です。
7. データ表示および分析技術
蓄積されたデータを可視化し、簡単に理解できる形式で表示する技術や、データから新たな知見を引き出す分析技術は、意思決定の質を向上させます。
8. 自律化技術
蓄積データを基に自動判断し、制御を行う自律化技術は、製造工程の効率化と柔軟性の向上に貢献します。
製造業におけるセキュリティリスクへの対応
製造業における情報セキュリティリスクは年々増加しており、企業はこれに対して包括的な対策を講じる必要があります。外部からのサイバー攻撃は依然として大きな脅威ですが、近年では内部不正による情報漏えいも深刻な問題となっています。2023年1月にIPAが公表した「情報セキュリティ10大脅威」では、”内部不正による情報漏えい”が第4位にランクインしており、この問題への対応が急務となっています。
内部不正の難しさと対応策 内部不正は、正規のアクセス権を持つ者によって行われることが多く、その防止は非常に困難です。「手土産転職」や産業スパイによる機密情報の漏えいが続発しており、このような内部リスクへの対策は組織全体で取り組む必要があります。アクセス権限の厳格な設定に加え、行動監視や異常検知システムの導入が求められます。
例えば、ソフトバンク元社員による5G営業秘密の不正持ち出し事件では、機密情報の漏えいが問題となり、内部不正対策の重要性が再認識されました【参考リンク】。これにより、従業員教育や監視体制の強化が、製造業におけるセキュリティリスクの軽減に不可欠であることが明らかになっています。
データコンサルタントとしては、製造業のネットワーク化やデータ活用を推進する一方で、セキュリティリスクへの包括的な対応を提案し、企業の持続可能な成長を支援します。
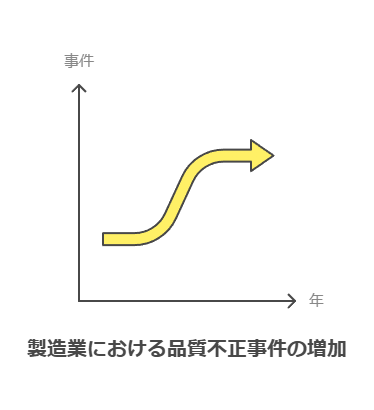
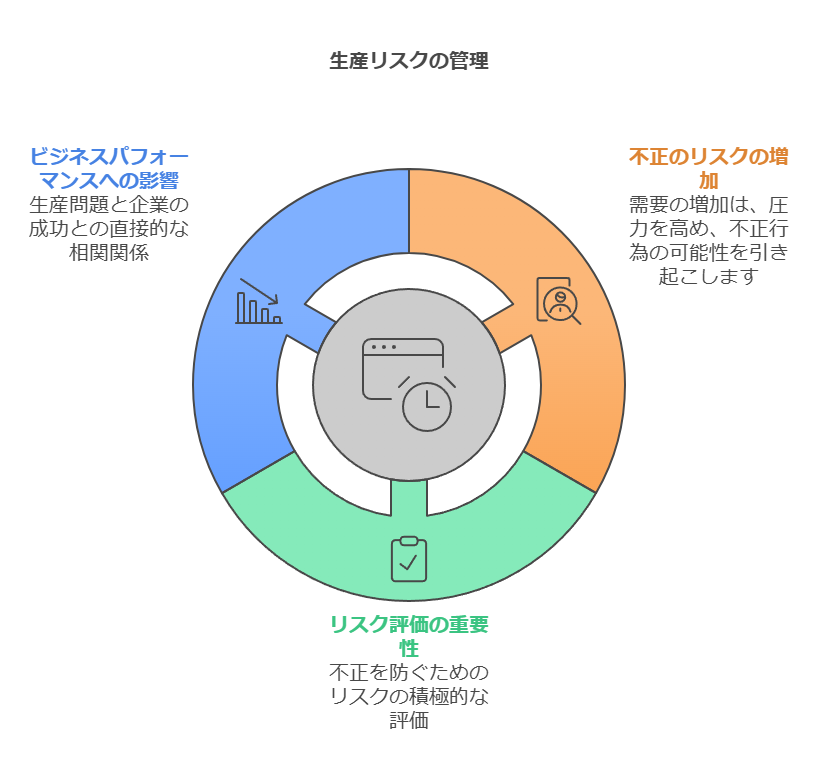
工場設備保全とデジタル化への取り組み
工場設備保全のご担当者や生産管理のご担当者が取り組んでいる設備稼働監視、工場生産管理、現場映像監視、計測器のIoT化などの取り組みは、生産効率を向上させるためにますます重要になっています。
防爆エリアにおけるデジタル化の課題
しかし、可燃性ガスや危険物を取り扱う施設では「防爆エリア」として厳格に管理されており、デジタル化、特にリモート保全の実現には多くの課題が存在します。これらのエリアでは、わずかな火花や熱が燃焼や爆発を引き起こす可能性があるため、通常の電子機器の使用は制限されます。そこで、防爆基準に準拠した特殊な機器やシステムを選定する必要があります。
防爆対応デバイスによるリモート保全の実現
こうした危険物を扱う施設において、安全性と業務効率化を両立させるためには、防爆対応デバイスの導入が不可欠です。例えば、設備の振動や温度を測定して故障を予測する防爆基準に対応した振動無線センサー、機械学習を活用したアナログ計器の自動読み取りを行うIoTカメラ、作業員の位置を把握するためのソリューション、防爆エリア内で使用可能な無線アクセスポイントやスマートフォン、そして一般のスマートデバイスを防爆エリアで利用可能にするモバイルデバイス用防爆ケースなどがあります。
データの集約とスマートファクトリ化への支援
これらのデバイスから収集されたデータは、IIJ産業IoTセキュアリモートマネジメント(SRM)を通じて集約され、データの可視化や分析が可能になります。また、これにより製造業の基幹システムとの統合もスムーズに行えるため、スマートファクトリ化の実現に向けた包括的な支援が提供されます。
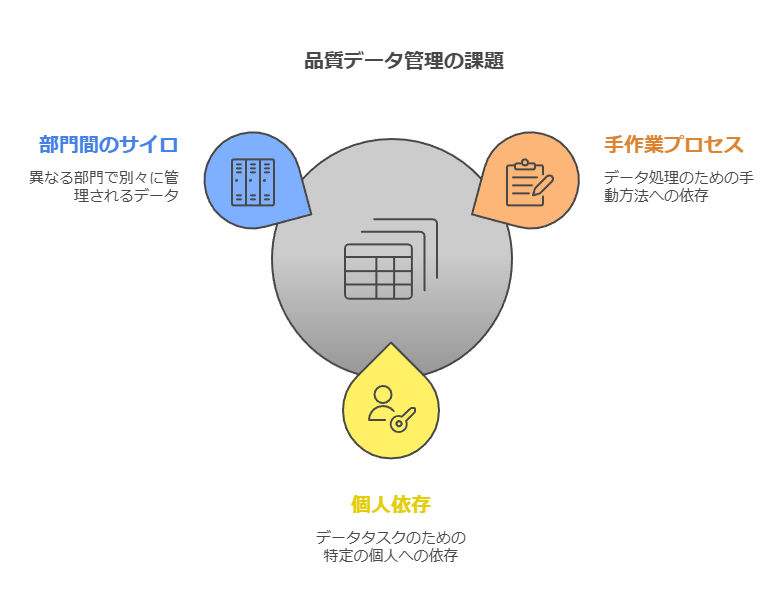
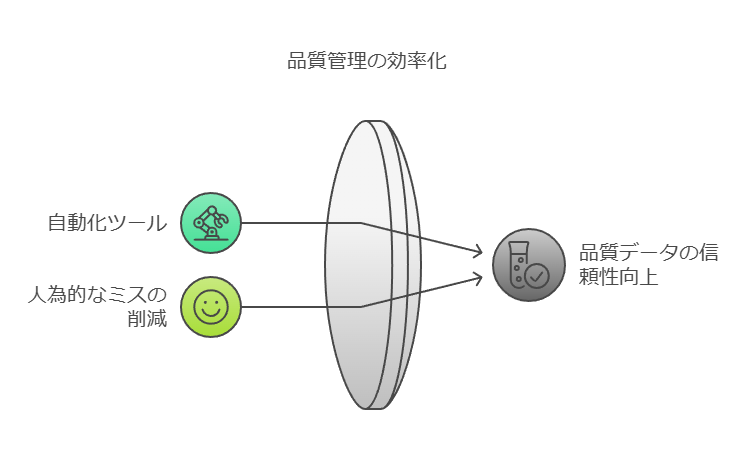
OT資産管理と脆弱性管理の重要性と課題
近年、OT資産に対するサイバー攻撃が増加しており、これらの資産管理や脆弱性の特定・対応が急務となっています。しかし、実際に管理を行う際には、どのツールを導入し、どのように運用すれば良いのか具体的なイメージが湧かない担当者も少なくないでしょう。当セッションでは、OT資産を効果的に管理する方法と、日々の運用を効率的に回すための具体的な事例やデモを交えながら解説します。
OT環境における資産管理とリスク管理の基本
まず、平時のOT環境の状態を正確に把握することが、効果的な資産管理とリスク管理の基礎となります。工場内で利用されているタワー型サーバの主要メーカーとして、以下の企業が挙げられます:
デル・テクノロジーズ(PowerEdgeなど)
NEC(Express5800など)
富士通(PRIMERGYなど)
日本アイ・ビー・エム(IBM Powerなど)
日本ヒューレット・パッカード(ProLiantなど)
レノボ・ジャパン(ThinkSystemなど)
保全人員の不足とIoT技術の活用
特に、石油プラントや化学工場などの危険物を扱う施設では、設備の老朽化や保全人員の不足、熟練技術者の減少が深刻な課題となっています。これらの問題により、適切な保守・メンテナンスが実施されず、火災事故のリスクが高まるケースも少なくありません。これに対処するためには、設備や機器の異常を早期に発見する仕組みが必要ですが、従来は作業員の経験に依存しており、広範囲に分散する設備の点検には時間と労力がかかっていました。このような背景から、IoT技術を活用して設備データを自動的に収集し、リアルタイムで監視する「リモート保全」の導入が求められています。
IoTセキュアリモートマネジメントによるスマートファクトリの実現
当社が提供する「IoTセキュアリモートマネジメント(SRM)」は、産業領域におけるIoTソリューションをワンストップで実現するためのサービスです。工場内設備のPLC/CNC、各種センサーからデータを収集するゲートウェイデバイス、セキュアな通信サービス、そして可視化・分析を行うクラウドまでを包括的に提供し、スマートファクトリの実現を強力に支援します。これにより、データの有効活用と効率的な運用が可能となり、工場全体の生産性向上を促進します。
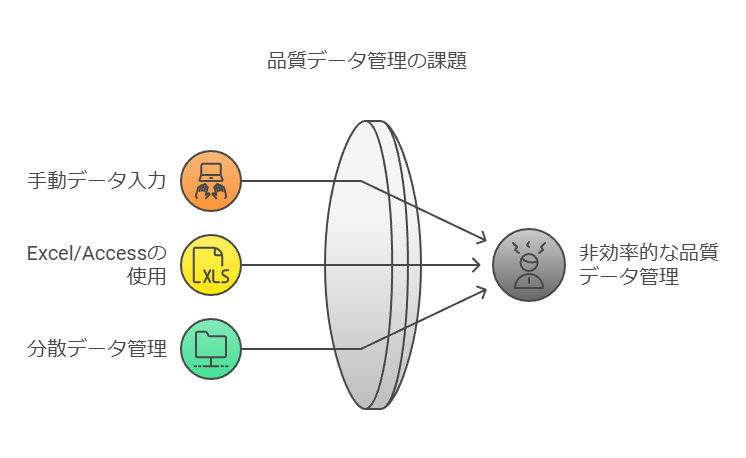
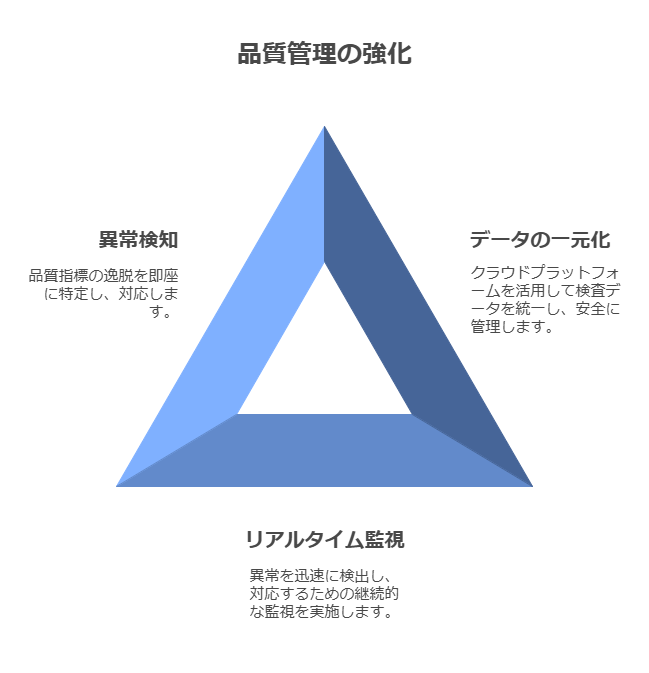
製造業におけるサイバーセキュリティの脅威の拡大
警察庁が発表した「サイバー空間をめぐる脅威の情勢等」によれば、製造業に対するランサムウェア攻撃の被害件数は、2021年の55件から2022年には75件へと大幅に増加しています。これは、製造業が先進的な技術導入やIoTの普及を進める中で、セキュリティリスクが急速に拡大していることを示しています。
特に注目すべきは、マルウェア感染やシステム侵害といった攻撃が、製造活動に大きな影響を与える可能性がある点です。これらの攻撃によって生産が遅延し、最悪の場合には大規模な生産停止に至ることも考えられます。さらに、現代の製造業ではサプライチェーンが高度に複雑化しているため、一度のサイバー攻撃が取引先全体に波及し、大きなリスクを引き起こす可能性が高まっています。
コロナ禍を契機とした製造現場における位置情報の活用
コロナ禍を経て、製造業におけるデジタルトランスフォーメーション(DX)が加速する中で、工場内のデータ可視化に位置情報を活用するケースが急増しています。日本プラントメンテナンス協会が実施した「2020年度メンテナンス実態調査概要」によると、2020年の製造業において「3年以内に投資が決定している技術」の中で、位置情報の活用ポイントは前年から約2倍に急増しています。
この背景には、コロナ禍における厳しい状況下で、「生産性の向上」や「安全面の確保」を目的とした抜本的な対策が求められていることが挙げられます。位置情報の活用は、製造現場における生産効率の最適化や安全性の向上を実現するための重要な要素となっており、今後もその重要性はますます増していくと考えられます。
データコンサルタントの視点では、セキュリティリスクと技術投資の動向を俯瞰し、具体的なリスク対策やデータの活用戦略が重要と判断しました。
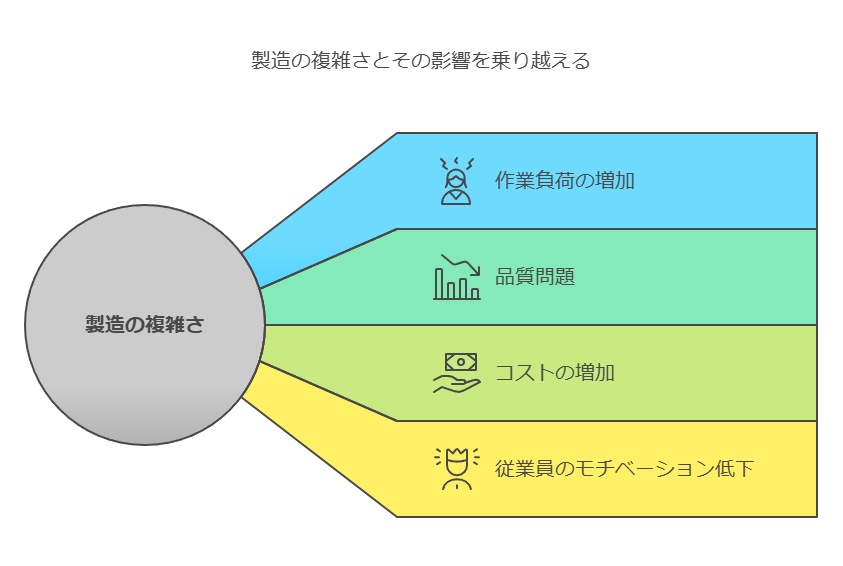
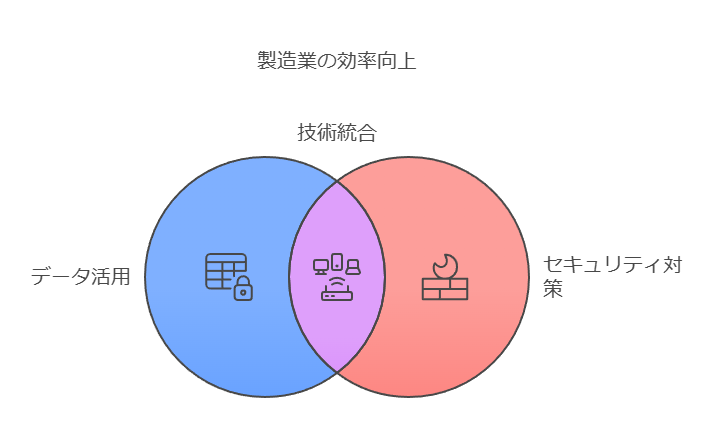
動態情報の可視化によるデータドリブンな議論の実現
これまで、工場内での人の行動、機器や車両の稼働、物の移動といった情報は、経験や感覚に頼って管理されてきました。しかし、これらの動態情報や稼働情報をデータとして可視化し、定量化することで、従来の直感に頼った管理から、より多くの「気づき」が得られるようになります。
データを定量的に扱うことで、全員が同じ基盤に立って議論できるようになり、意思決定の質が向上します。これにより、建設的かつ効果的なディスカッションが可能となり、組織全体の生産性が向上します。
実際の導入事例:可視化による生産性向上の成果
弊社が支援したお客様の事例では、ヒトやモノの移動を可視化し、以下のような具体的な成果を上げています。
作業効率の向上: 作業効率が37%向上し、必要な人員を10名から9名に削減。
車両管理の最適化: 稼働中の約80台の車両から10台を削減。
製造リードタイムの短縮: リードタイムを26%短縮し、仕掛かり在庫数を60%削減。
ヒトの行動を可視化するためのアプローチ
ヒトやモノの行動を可視化するためには、次のような技術と方法を活用します。
測位技術の選定と精度管理: 目的に応じた測位技術を選定し、測定誤差を最小限に抑える。
データ分析機能の活用: データの収集・分析機能を活用して、行動パターンや稼働状況を可視化。
屋内外でのシームレスな測定: 工場内外をシームレスに測定するための技術。
センサー情報による稼働管理: センサー情報を活用して、機器や車両の稼働状況をリアルタイムで管理。
こんな方におすすめ
次のような課題やニーズをお持ちの方に、このアプローチを特におすすめします。
工場の規模が大きく、現場の状況把握に課題がある方
既に機器データの取得と最適化を行っているが、さらなる生産性向上を目指している方
IoTを活用してデジタルトランスフォーメーション(DX)を進めたいが、何から始めるべきか分からない方
データコンサルタントとしては、データの可視化を通じて、現場の課題を明確にし、具体的な改善策を提案することが重要です。また、具体的な事例を通じて、データドリブンなアプローチがいかに効果的であるかを示すことが、企業の意思決定を支援するための鍵となります。
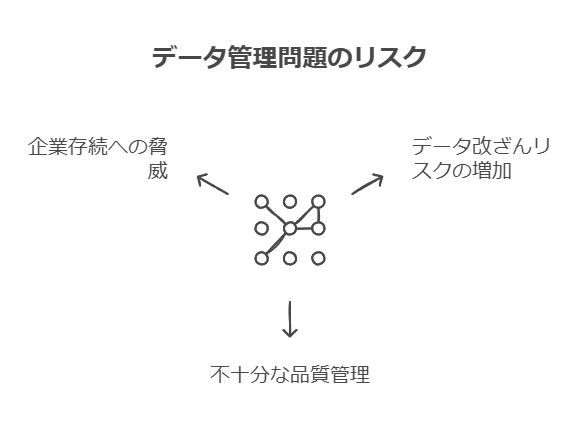
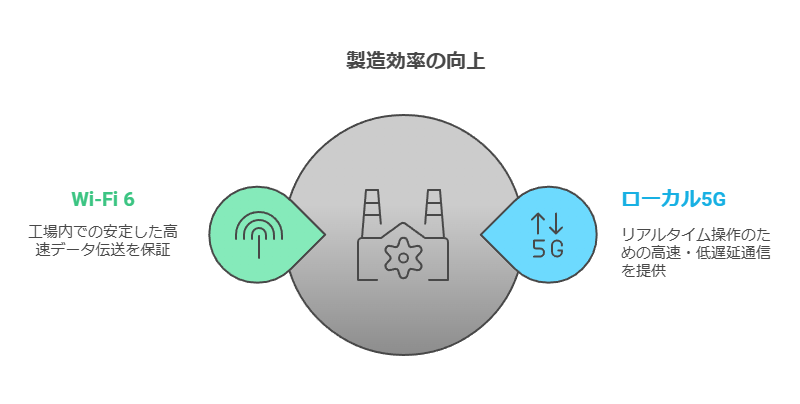
製造業の人材不足と高齢化が引き起こす外観検査の限界
製造業において、深刻な人材不足と従業員の高齢化が顕著になっています。特に、熟練技能を持つ人材の減少は、企業の競争力に大きな影響を与えています。その中でも、熟練した従業員による外観検査の継続が困難になりつつあり、従来の目視検査は、検査員の経験や体調に左右されるため、品質のばらつきが発生しやすくなっています。このような背景から、目視による外観検査の限界が指摘されています。
外観検査の自動化に直面する課題とその解決策
外観検査の自動化は、多くの製造業が直面する課題への一つの解決策として注目されています。しかし、導入に際しては多くの企業がITリソースの不足に悩まされ、どのようなシステムを選定すべきか迷うケースが少なくありません。さらに、導入を決断した企業でも、期待していた検査精度に達せず、結果的に目視検査のダブルチェックが必要になることがあります。
こうした課題を解決するためには、AIを活用した柔軟で高度な外観検査システムの導入が鍵となります。特に、従来の画像処理センサーでは対応が難しかった個体差のある検査対象にも、AIの高度な判断基準を活用することで対応可能となり、精度と効率を両立させることができます。
外観検査結果のデータ活用による品質改善と歩留まり向上
外観検査で得られるデータは、品質改善における非常に重要な情報源です。このデータを分析することで、どの工程に問題があるのかを特定し、これまで手をつけることが難しかった歩留まり改善に取り組むことが可能です。さらに、シンプルな閾値調整機能やAIによる再学習機能を備えたシステムを活用することで、企業のニーズに応じた精度調整が可能となり、より効果的な品質管理が実現します。
AIによる次世代の外観検査サービスの導入支援
当社では、製造業におけるAIを活用した次世代の外観検査サービスを提供しています。これにより、製造現場の生産性向上と品質確保を支援し、競争力の強化を図ります。導入から運用、継続的な最適化まで、一貫したサポートを提供することで、企業が直面する課題を解決し、持続的な成長を支援します。
データコンサルタントとしては、企業が直面する技術的課題を分析し、データを活用したソリューションを提供することで、長期的な競争力の強化をサポートすることが重要です。AIやデータ分析技術を駆使して、製造業の品質管理や生産性向上に寄与する具体的な提案を行うことが求められます。
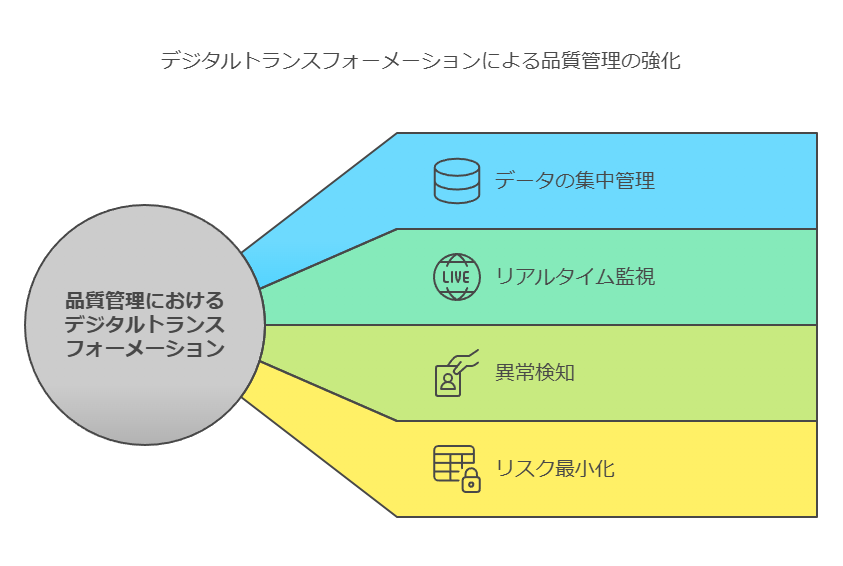
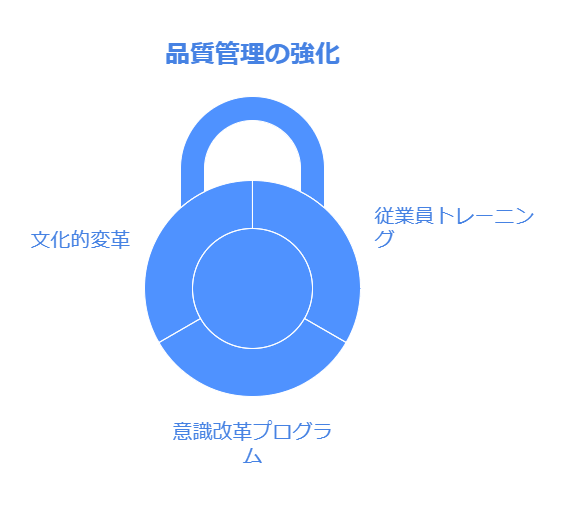
ボトムアップ型改善における「現場の壁」と全社最適化の課題
日本の製造業は、現場主導の改善活動が長く根付いており、特に三現主義(現場・現物・現実)を重んじる文化が強くあります。現場作業員が深い知識を持ち、日々の業務改善に積極的に取り組む姿勢は、製造ラインや特定の工程における局所的な最適化に大いに寄与してきました。しかし、このボトムアップ型の改善アプローチには、製造現場全体の最適化や、複数の工程を統合した広範な最適化、さらには工場を超えた全社的な最適化を進める際に「現場の壁」が存在します。
特に、長年にわたり確立された作業方法が深く根付いている現場では、新しいシステムやデータ活用の導入に対して不安や抵抗が生じることが多いです。この結果、短期的な効率性や現場のROI(費用対効果)が優先され、データを活用した長期的かつ全社的な最適化の推進が遅れるリスクがあります。
製造業DX実現のためのデータマネジメント戦略
製造業においてデジタルトランスフォーメーション(DX)を成功させるためには、現場に蓄積されたデータの価値を認識し、これを活用する重要性を現場にしっかりと伝えることが不可欠です。特に、今まで十分に活用されてこなかった製造現場データがもたらす全社的なメリットを明確に示すことで、現場の理解と協力を得ることが可能になります。
さらに、データ収集と分析プロセスにおいて現場社員が積極的に関与することが重要です。現場の視点を反映したデータの収集は、現場作業員がデータの重要性を「自分事」として受け入れる鍵となります。これにより、データ活用の意義が現場に浸透し、全社的な最適化が進む基盤を築くことができます。
次のステップ:データ活用による全社的最適化への道
データコンサルタントとしては、現場主導の改善を尊重しつつ、全社的な最適化を実現するためのデータマネジメント戦略を提案します。これには、現場と経営層が共通の目的を持ち、データの収集・活用を通じて組織全体の競争力を向上させるための継続的な取り組みが含まれます。データドリブンな意思決定を促進し、現場から経営層までが一体となって進めるDXの推進が、製造業における持続可能な成長の鍵となるでしょう。
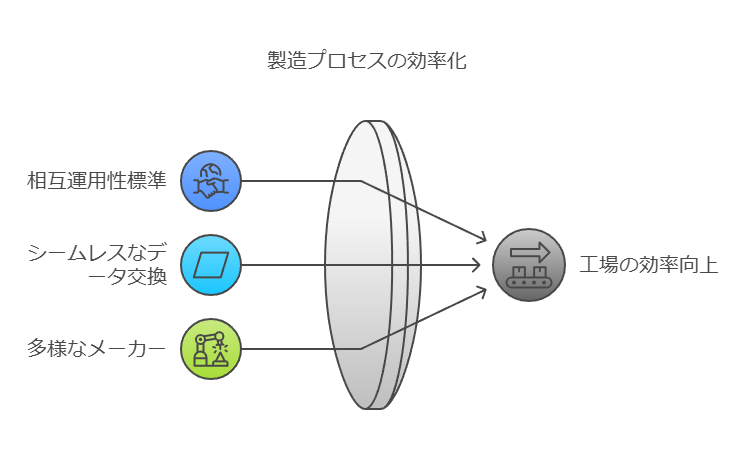
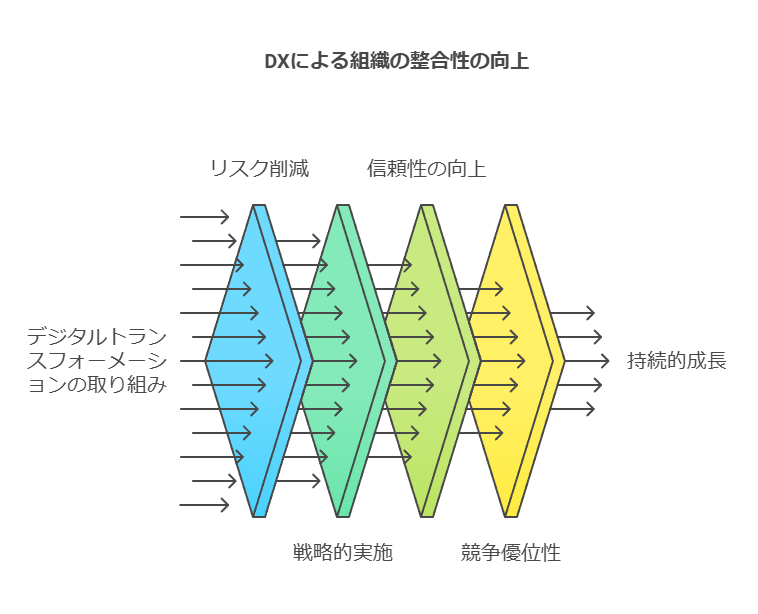
ペーパーレス化が進まない原因と課題
IoT化を推進する中で、ペーパーレス化を重要な施策の一つと考える方は多いでしょう。ペーパーレス化には、文書管理が容易になり、データの利活用によって業務改善が図れるといった多くの利点があります。しかし、ペーパーレス化の導入が目的化してしまったり、現場のデジタルリテラシーが追いつかず、形骸化するケースが散見されます。こうした状況は、導入効果が発揮されないまま、かえって業務の複雑化や混乱を招くリスクがあります。
現場で機能するペーパーレス化ソリューション
これらの課題を解決するためには、単なるデジタル化にとどまらず、現場で実際に活用されるソリューションが必要です。例えば、「ABookBiz」というペーパーレス化ソリューションは、現場のニーズに応じたデジタル化を実現します。このソリューションは、マニュアルやチェックシートをデジタル化するだけでなく、動画形式のマニュアルや、VRを活用したオプションの選択が可能です。これにより、機器にQRコードを配置し、必要な部分だけをピンポイントで閲覧するなど、現場の業務に直結した形でペーパーレス化を進めることができます。
また、WiFiが利用できないエリアでもオフラインでの利用が可能であり、強固なセキュリティを有しているため、安全にデータを管理・運用できる点が評価されています。業務効率化や標準化を目指す管理者・決裁者、あるいは提案しやすい商材をお探しのSIerやコンサルタントにとって、非常に有力なソリューションとなります。
現場主導のDXによる企業全体の最適化
ペーパーレス化は、単なるデジタル化ではなく、現場主導のデジタルトランスフォーメーション(DX)の一環として捉えるべきです。これにより、工程や生産ラインにとどまらず、工場や部門間の壁を取り払い、企業全体の最適化を実現することが可能となります。現場の声を反映したDXは、持続可能で効果的なビジネス変革を推進します。
製造業におけるサイバー攻撃の増加
製造業におけるサイバー攻撃は増加の一途を辿っており、警察庁が発表した「サイバー空間をめぐる脅威の情勢等」によれば、ランサムウェアによる攻撃被害は2021年の55件から、2022年には75件と大幅に増加しています。この脅威に対処するためにも、ペーパーレス化を含むデジタル化施策には、セキュリティ対策を組み込むことが不可欠です。データコンサルタントとしては、セキュリティを強化しつつ、効率的なペーパーレス化の導入支援を行うことが重要です。
ここでは、ペーパーレス化の推進が現場での課題解決にどのように貢献するかを明確にし、現場主導のDXの重要性を強調しています。また、セキュリティリスクに対する認識とその対策を強調することで、ペーパーレス化を包括的なビジネス改善の一環として捉えています。
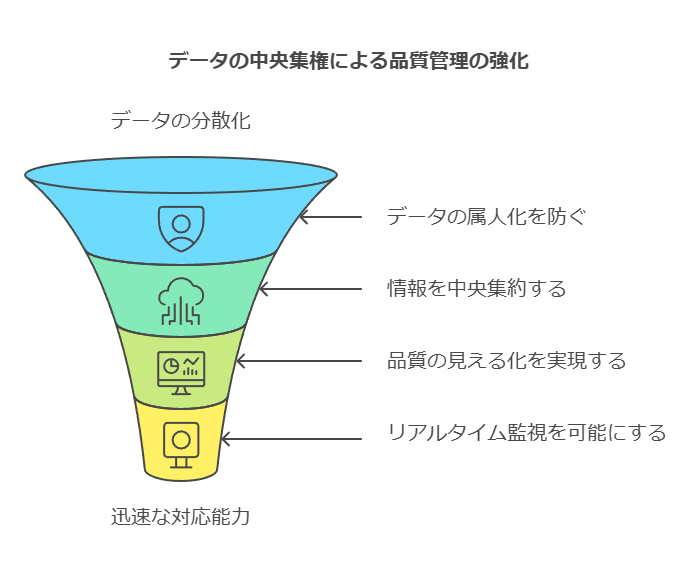
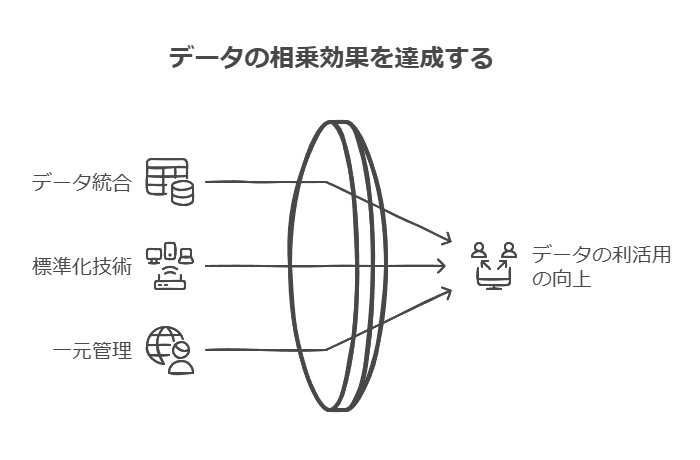